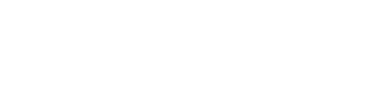
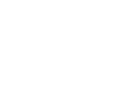
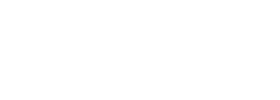
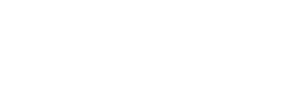
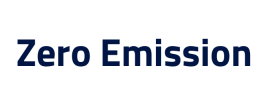

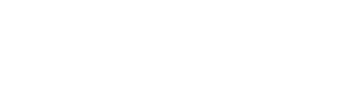
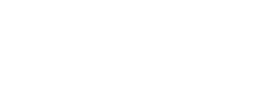
October 2024, no. 141
Zero Emisssion Lab
Zero Emission Services
www.marin.nl/jips/zero
More info
Effective decision making on upcoming alternative propulsion, power and energy (PPE) systems on ships
Interested? Contact us to discuss your options
Create a MARIN account to stay updated
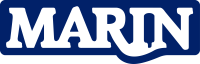
Figure 1: The W model consisting of the virtual design cycle (left) and actual building cycle (right).
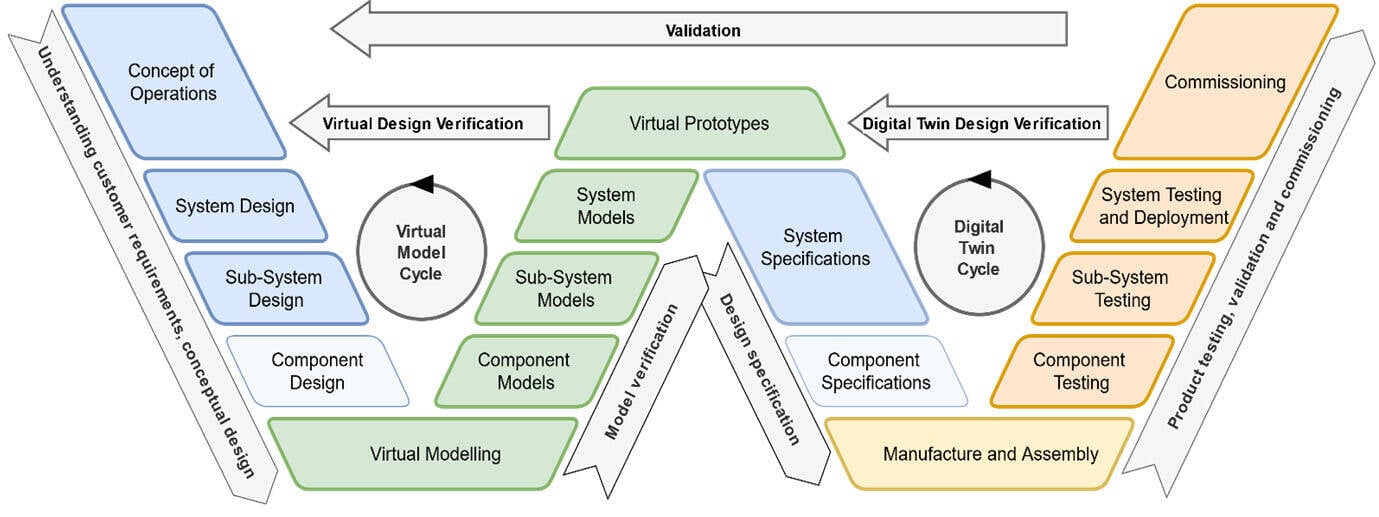
Report
Introducing MARIN’s Zero Emission Services
Areal view of the Zero Emission Lab for verification&validation of PPE designs, demonstration of PPE performance and Engine Room of the Future Experience room.
Design offices, shipping companies and shipyards are searching for cleaner ways to operate, but the variety of alternative energy solutions to choose from is wide and continuously developing. What emissions are produced during my operations? Which alternative energy and power technologies are available, feasible and affordable for my operations?
MARIN’s comprehensive Zero Emission Services can support the decision-making process when you’re considering the optimal zero emission strategy for your fleets.
Understanding the real - in service - energy needs and system preferences of operators is essential. Usually, the first step is to ensure that the hull and propulsion are optimised to reduce energy needs using traditional techniques. Nowadays, we also include a technology trade-off study where power and energy technologies, alternative operations or wind propulsion are considered.
Scenario simulations are a powerful method to evaluate future or alternative designs in authentic operational conditions, supported by hindcast environmental data. Using virtual models of the PPE system and ship we can assess the performance of individual ships and also fleet performance and energy infrastructure requirements.
Recently, MARIN constructed the ‘NEEDS’ environment; a scenario simulation model, including dynamic techno-economic components, that can allow policymakers, regional and national authorities, ship and fleet owners, harbour and energy suppliers, to launch alternative scenarios based on their current operations and power and energy system choices. (See also article on NEEDS Simulation Framework).
The model includes the energy supply, harbour infrastructures (energy bunkering, charging or swapping and shipping logistics), ships, cargo capacity, waterborne operations and the environmental conditions. Coupled with long-term hindcast data, this allows us to run scenarios and assess implementation strategies for the coming decades.
The involvement of the future crew in the design of the ship and its operation is a prerequisite for safe, effective and smart ships and offshore structures. With a coupling between the Seven Oceans Simulation centre (SOSc) and the vZEL or ZEL, the interaction between the user and the PPE system can be experienced and analysed and Human Machine Interfacing and PPE Control & Automation can be further improved.
Design verifications can also be done on existing systems and is often done in the case of troubleshooting on ships in service. MARIN offers comprehensive support with our team of naval architects, mechanical, electrical, control & automation specialists, onboard measuring specialists and hydrodynamic experts. Linking in-service data to our virtual models we can analyse a ship’s performance and provide a quick solution to many operational challenges.
Fig 2. Simulation results of a 25 m inland patrol vessel on a typical day mission.
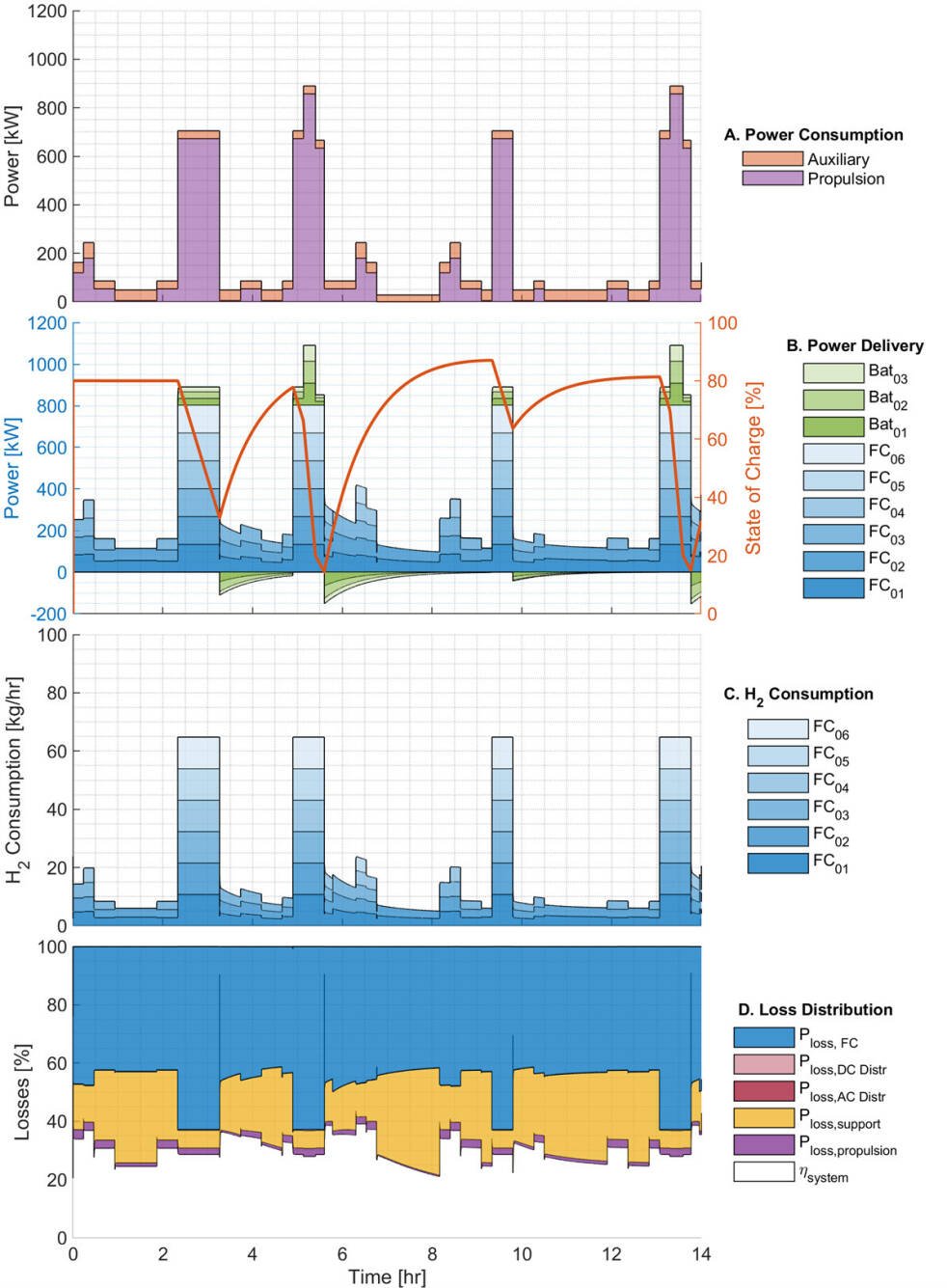
Improved PPE system design
Based on the results, battery and fuel cell sizing could be verified. We observed a significantly lower efficiency of the full PPE plant, resulting in higher hydrogen consumption than assumed in the PPE design phase. This was mainly due to the higher power needs of the supporting systems.
The results of all the test cases provided input for an updated and improved PPE system design. That design is the starting point of the right side of the W model: system realisation and commissioning. In this phase, MARIN can assist the sector with digital twinning and physical system verification to give a few examples. This all serves to highlight how MARIN supports the industry in realising reliable and robust Zero Emission solutions.
ZERO JIP
As part of the ZERO JIP, MARIN has evaluated the performance of a 25 m inland patrol vessel equipped with a Hydrogen Fuel Cell Electric PPE system with 6 fuel cells and a battery system for dynamic support. Test case simulations are performed to evaluate system performance and overall hydrogen use for long-range patrol, sailing in waves, turning circle manoeuvres, crash stops, etc. Fig 2 gives a typical example of simulation results of a full-day mission, based on a predefined power profile derived from full scale measurements on a similar conventionally powered vessel.
The top graph shows the propulsion and auxiliary power that is required during the one-day mission. The second graph shows how the PPE system provides that power, the contribution of the fuel cells, batteries and battery recharging cycles. The spread of the power production over the different PPE components depends on choices made in the power and energy management system (EMS). Typically, several EMS strategies are constructed and compared. The third graph provides the actual hydrogen consumption, while the bottom graph shows the instantaneous system efficiency (the bottom white part) and the losses that are active in the PPE system components. Note, at low power demand the support power is still considerable, lowering the system performance. At high power demand the fuel cell losses are more pronounced.
In the right leg of the Virtual Model Cycle (green lane) the PPE system is modelled for performing simulations and tests to eventually verify the design. The virtual tests mitigate the risks involved when building highly innovative vessels and can lead to refined design specifications. MARIN supports this process by employing simulations and scaled-physical tests in our virtual and physical Zero Emission Lab, respectively.
Virtual Zero Emission Lab
The virtual Zero Emission Lab (vZEL) is a modelling platform with an extensive set of mathematical models of PPE system components, where virtual representations of the designed system can be configured and tested. The model library consists of models with varying levels of complexity and fidelity and the appropriate models are chosen based on the tests to be performed. The PPE system model can be coupled to MARIN’s hydrodynamic (XMF) models for simulations where the performance of the design can be simulated and analysed in various conditions.
Physical Zero Emission Lab
The physical Zero Emission Lab (ZEL) contains the
physical hardware for a future-ready engine room. Typical power components available are a hydrogen fuel cell, super capacitors and an internal combustion engine generator set that can run on methanol. These can be extended using emulated components where vZEL models are used to emulate their behaviour. Additionally, the ZEL includes supporting components such as the storage for energy carriers, electrical infrastructure in DC and AC, advanced automation and control systems, and integrated cooling. The engine room hardware connects to the hydrodynamics through a propeller in our cavitation tunnel and an additional electric machine that can impose load variations to waves and manoeuvres for example. Besides propulsion, several auxiliary and payload consumers can be configured including hoisting and dredging operations.
A design can be put through its paces in a realistic operational environment to test system performance and integration. It also serves as a demonstration, experience and training environment where innovative PPE system designs can be experienced by future operators and technicians.
By accounting for all these aspects in an early design stage the propulsion, power and energy system is made and matched with the intended operations. This forms the basis of the PPE system integration. System layout and interfaces are based upon requirements from class, control and operability and technical dependencies of components.
PPE system design and verification
With the operational requirements in place and the preferred technology chosen, we create different PPE configurations, which can be compared and assessed on a variety of aspects such as the expected efficiencies and reliability. This results in a layout with the sizing of components and the principal component interfaces. This concept design can be considered as a virtual prototype which is depicted in the so-called ‘W model’ (see Fig 1). The right part of the W model represents the conventional V model for building projects. The left represents the creation of the virtual prototype which is the base for the digital twin of the vessel.
Video test case 2: Simulation showing the difference between shaft speed and torque control on the overall PPE and ship performance.
Video test case 1: Simulation of a surface combatant firing a high-power weapon during a manoeuvre.
Zero Emission Services
Zero Emisssion Lab
Improved PPE system design
Based on the results, battery and fuel cell sizing could be verified. We observed a significantly lower efficiency of the full PPE plant, resulting in higher hydrogen consumption than assumed in the PPE design phase. This was mainly due to the higher power needs of the supporting systems.
The results of all the test cases provided input for an updated and improved PPE system design. That design is the starting point of the right side of the W model: system realisation and commissioning. In this phase, MARIN can assist the sector with digital twinning and physical system verification to give a few examples. This all serves to highlight how MARIN supports the industry in realising reliable and robust Zero Emission solutions.
Fig 2. Simulation results of a 25 m inland patrol vessel on a typical day mission.
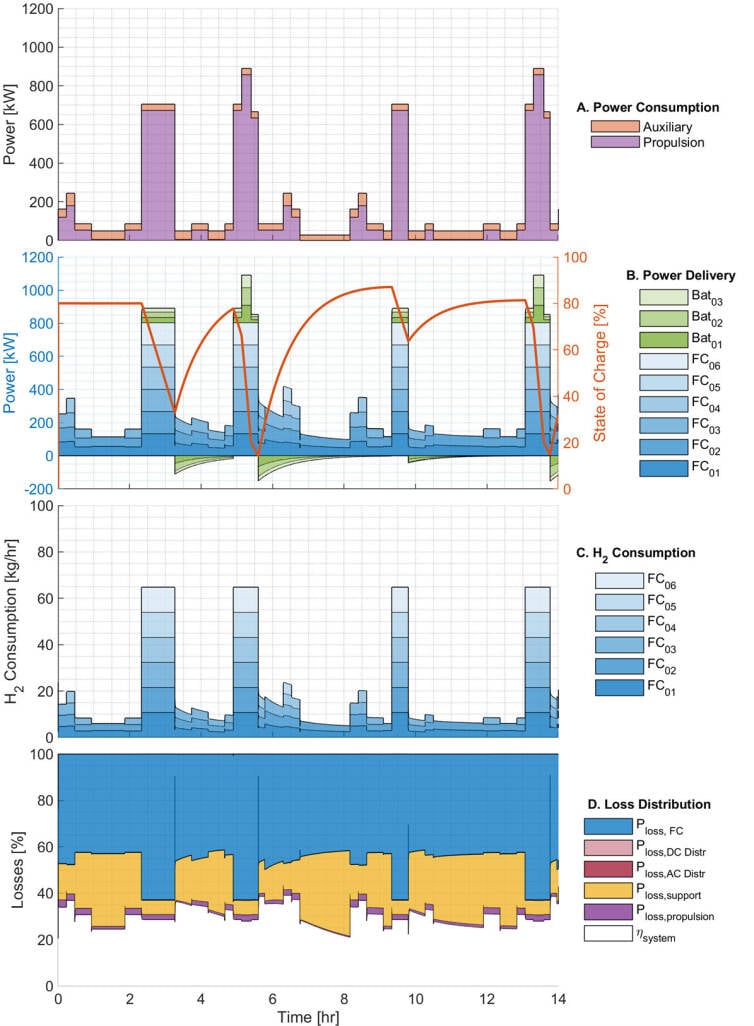
October 2024, no. 141
ZERO JIP
As part of the ZERO JIP, MARIN has evaluated the performance of a 25 m inland patrol vessel equipped with a Hydrogen Fuel Cell Electric PPE system with 6 fuel cells and a battery system for dynamic support. Test case simulations are performed to evaluate system performance and overall hydrogen use for long-range patrol, sailing in waves, turning circle manoeuvres, crash stops, etc. Fig 2 gives a typical example of simulation results of a full-day mission, based on a predefined power profile derived from full scale measurements on a similar conventionally powered vessel.
The top graph shows the propulsion and auxiliary power that is required during the one-day mission. The second graph shows how the PPE system provides that power, the contribution of the fuel cells, batteries and battery recharging cycles. The spread of the power production over the different PPE components depends on choices made in the power and energy management system (EMS). Typically, several EMS strategies are constructed and compared. The third graph provides the actual hydrogen consumption, while the bottom graph shows the instantaneous system efficiency (the bottom white part) and the losses that are active in the PPE system components. Note, at low power demand the support power is still considerable, lowering the system performance. At high power demand the fuel cell losses are more pronounced.
Areal view of the Zero Emission Lab for verification&validation of PPE designs, demonstration of PPE performance and Engine Room of the Future Experience room.
More info
www.marin.nl/jips/zero
Interested? Contact us to discuss your options
In the right leg of the Virtual Model Cycle (green lane) the PPE system is modelled for performing simulations and tests to eventually verify the design. The virtual tests mitigate the risks involved when building highly innovative vessels and can lead to refined design specifications. MARIN supports this process by employing simulations and scaled-physical tests in our virtual and physical Zero Emission Lab, respectively.
Virtual Zero Emission Lab
The virtual Zero Emission Lab (vZEL) is a modelling platform with an extensive set of mathematical models of PPE system components, where virtual representations of the designed system can be configured and tested. The model library consists of models with varying levels of complexity and fidelity and the appropriate models are chosen based on the tests to be performed. The PPE system model can be coupled to MARIN’s hydrodynamic (XMF) models for simulations where the performance of the design can be simulated and analysed in various conditions.
Physical Zero Emission Lab
The physical Zero Emission Lab (ZEL) contains the
physical hardware for a future-ready engine room. Typical power components available are a hydrogen fuel cell, super capacitors and an internal combustion engine generator set that can run on methanol. These can be extended using emulated components where vZEL models are used to emulate their behaviour. Additionally, the ZEL includes supporting components such as the storage for energy carriers, electrical infrastructure in DC and AC, advanced automation and control systems, and integrated cooling. The engine room hardware connects to the hydrodynamics through a propeller in our cavitation tunnel and an additional electric machine that can impose load variations to waves and manoeuvres for example. Besides propulsion, several auxiliary and payload consumers can be configured including hoisting and dredging operations.
A design can be put through its paces in a realistic operational environment to test system performance and integration. It also serves as a demonstration, experience and training environment where innovative PPE system designs can be experienced by future operators and technicians.
Video test case 2: Simulation showing the difference between shaft speed and torque control on the overall PPE and ship performance.
Video test case 1: Simulation of a surface combatant firing a high-power weapon during a manoeuvre.
Figure 1: Experiment: comparison between VR (above) and physical interaction (under) simulations.
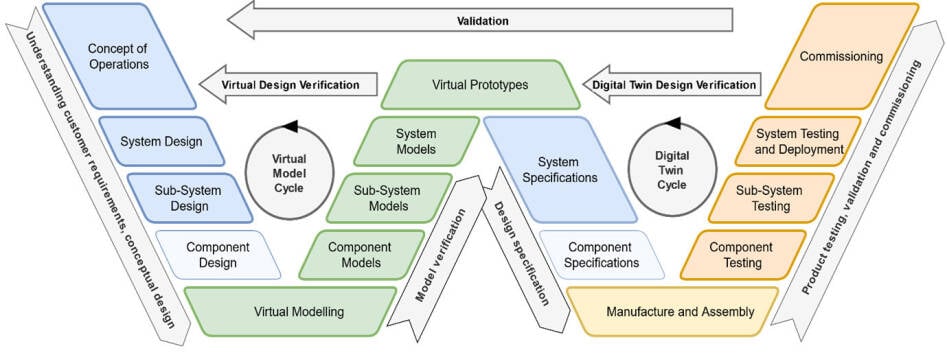
By accounting for all these aspects in an early design stage the propulsion, power and energy system is made and matched with the intended operations. This forms the basis of the PPE system integration. System layout and interfaces are based upon requirements from class, control and operability and technical dependencies of components.
PPE system design and verification
With the operational requirements in place and the preferred technology chosen, we create different PPE configurations, which can be compared and assessed on a variety of aspects such as the expected efficiencies and reliability. This results in a layout with the sizing of components and the principal component interfaces. This concept design can be considered as a virtual prototype which is depicted in the so-called ‘W model’ (see Fig 1). The right part of the W model represents the conventional V model for building projects. The left represents the creation of the virtual prototype which is the base for the digital twin of the vessel.
MARIN’s comprehensive Zero Emission Services can support the decision-making process when you’re considering the optimal zero emission strategy for your fleets.
Understanding the real - in service - energy needs and system preferences of operators is essential. Usually, the first step is to ensure that the hull and propulsion are optimised to reduce energy needs using traditional techniques. Nowadays, we also include a technology trade-off study where power and energy technologies, alternative operations or wind propulsion are considered.
Design offices, shipping companies and shipyards are searching for cleaner ways to operate, but the variety of alternative energy solutions to choose from is wide and continuously developing. What emissions are produced during my operations? Which alternative energy and power technologies are available, feasible and affordable for my operations?
Effective decision making on upcoming alternative propulsion, power and energy (PPE) systems on ships
Introducing MARIN’s Zero Emission Services
Create a MARIN account to stay updated
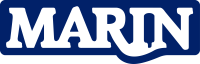
Report