The new wireless measurement system µMMS used to test Hyundai Heavy Industries Hi-Float 15MW floating wind turbine in the Offshore basin.
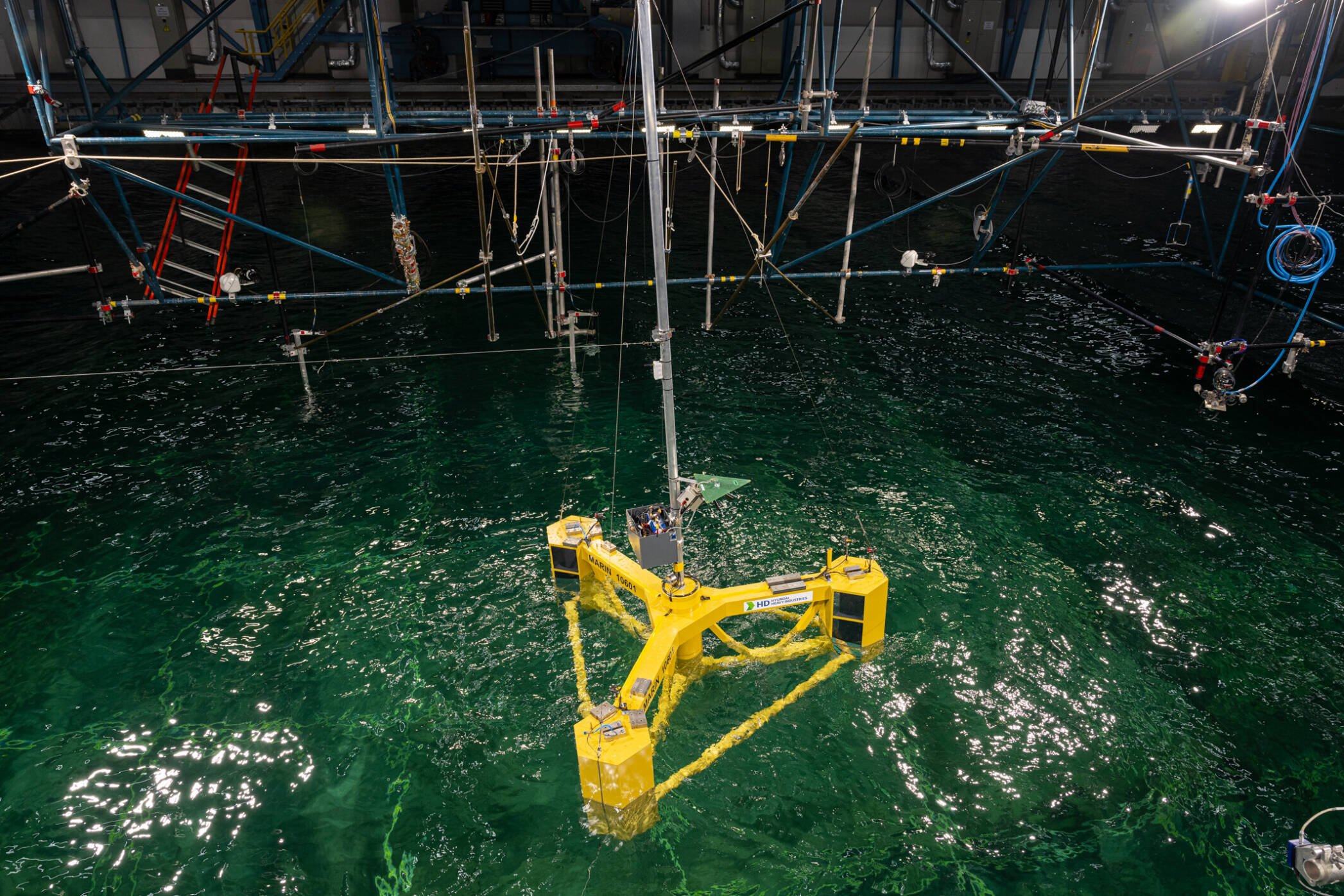
Interested? Contact us to discuss your options
The µMMS (Micro MARIN Measurement System) is specifically designed for light floaters, which means the measurement system is very light and small, such that it can easily be installed on a FOWT model.
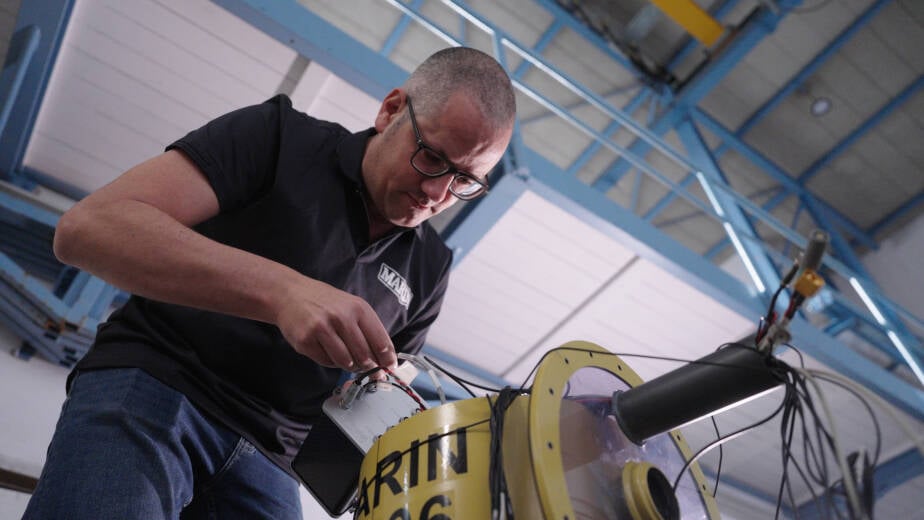
µMMS
(Micro MARIN Measurement System)
Universal analog sensor signal conditioning: Bridge, IEPE, Voltage
Local data storage or real-time streaming over ethernet (WiFi)
Programmable sampling rates & anti-alias filters
Irig time synchronisation (in sync with other MARIN systems)
Supports sensor ID for PnP
Dimensions: 15 x 12 x 17 cm
Weight: 1.3kg
Ingress protection: IP65
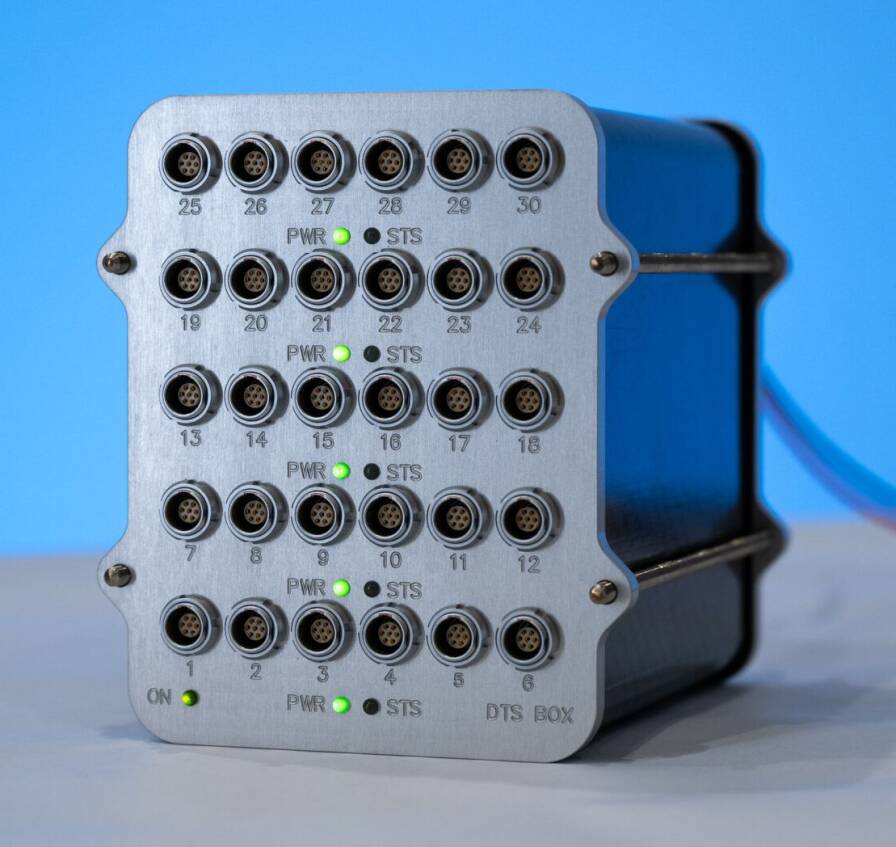
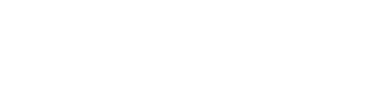
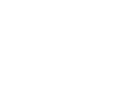
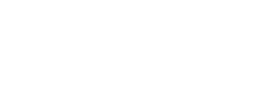
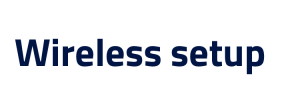
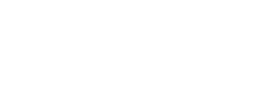
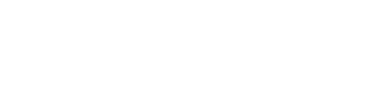
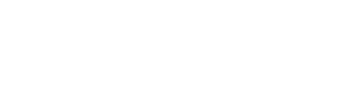
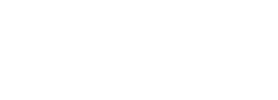
Better Ships, Blue Oceans
More info
www.marin.nl/sosc
October 2024, no. 141
Create a MARIN account to stay updated
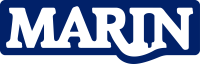
The µMMS is not only applicable for FOWT, but also for other small floaters and ships. The new measurement system makes it possible to accurately test small vessels, without the unwanted effect of the measurement cables.
For example, this year the Dutch Ministry of Infrastructure and Water Management contracted MARIN to investigate the dynamics that are involved in the capsizing of beam trawlers. The main goal of this project was to investigate the capsize risk in relation to fishing operations and the stability criteria.
Initially, we had planned to make a free sailing model for the tests that connects to the measurement system on the carriage. The combination of a small vessel and the high wave height in the tests resulted in a model weight of less than 100 kg. Given the small model size, low forces can have an impact on the rolling behaviour of the vessel. Therefore, to minimise the impact that the cables can have on the motions of the vessel, we minimised the number of sensors on board to the bare minimum. Additionally, we planned to use thinner cables than normal to reduce the weight even further.
The µMMS became available when we were designing the model. This offered the opportunity to make the model completely wireless and to measure more signals within the budget of the project. Without the measurement wires between the carriage and the model, the test setup was more versatile. No precautions were necessary to avoid interference from the measurement cables.
µMMS system available for clients
To mitigate this unwanted effect of the measurement cables, MARIN has developed a wireless measurement system called µMMS (Micro MARIN Measurement System). The system is specifically designed for light floaters, which means the measurement system is very light and small, such that it can easily be installed on a FOWT model. Furthermore, the system works on a battery pack and has real-time communication with the carriage so the basin crew can monitor the measurements during a model test.
The new wireless measurement system is now available for our clients, as well as a broad range of other comprehensive solutions for model testing floating turbines.
Increasing instrumentation
In the last decade we have seen that the amount of instrumentation on FOWT models has increased significantly, so we don’t merely measure motions and mooring line loads, but also additional signals such as impact loads, loads on the heave plate and internal loads. The growing amount of instrumentation on the models also has a significant downside, as the measurement cables are typically connected to the (earth fixed) carriage.
Especially for FOWT, this effect can be significant as these types of floaters are typically (very) light. Furthermore, it is difficult to quantify the effect of the cables on the dynamic floater motions and eigen periods. Although mitigating measures are taken by using light and flexible cables, the effect cannot be completely taken away.
A key point of model testing floating wind turbines is that wind and waves are presented simultaneously in the basin. This makes it possible to correctly study the complex motions and loads of the rotating turbine on a moving platform in wind and waves. For the first model tests with FOWT, no dedicated test setup was available, which resulted in using the existing test setup for oil & gas floaters.
However, over time, tailored model test techniques were developed specifically for model testing floating turbines. At first, these mainly focused on modelling the aerodynamic loading on the FOWT in the basin by developing high quality wind in the offshore basin, and different sizes of stock wind turbines. Alongside this, other aerodynamic modelling approaches were developed, whereby the loads are applied using either winches or small ducted fans as actuators controlled by aerodynamic BEM models.
Report
New wireless measurement setup for floating offshore wind turbines
MARIN has been involved in floating wind turbines (FOWT) right from the start, when the early pioneers started to develop the technology around 20 years ago. But in the last decade we have really seen the market getting more mature, shifting the projects from the concept to the design stage.
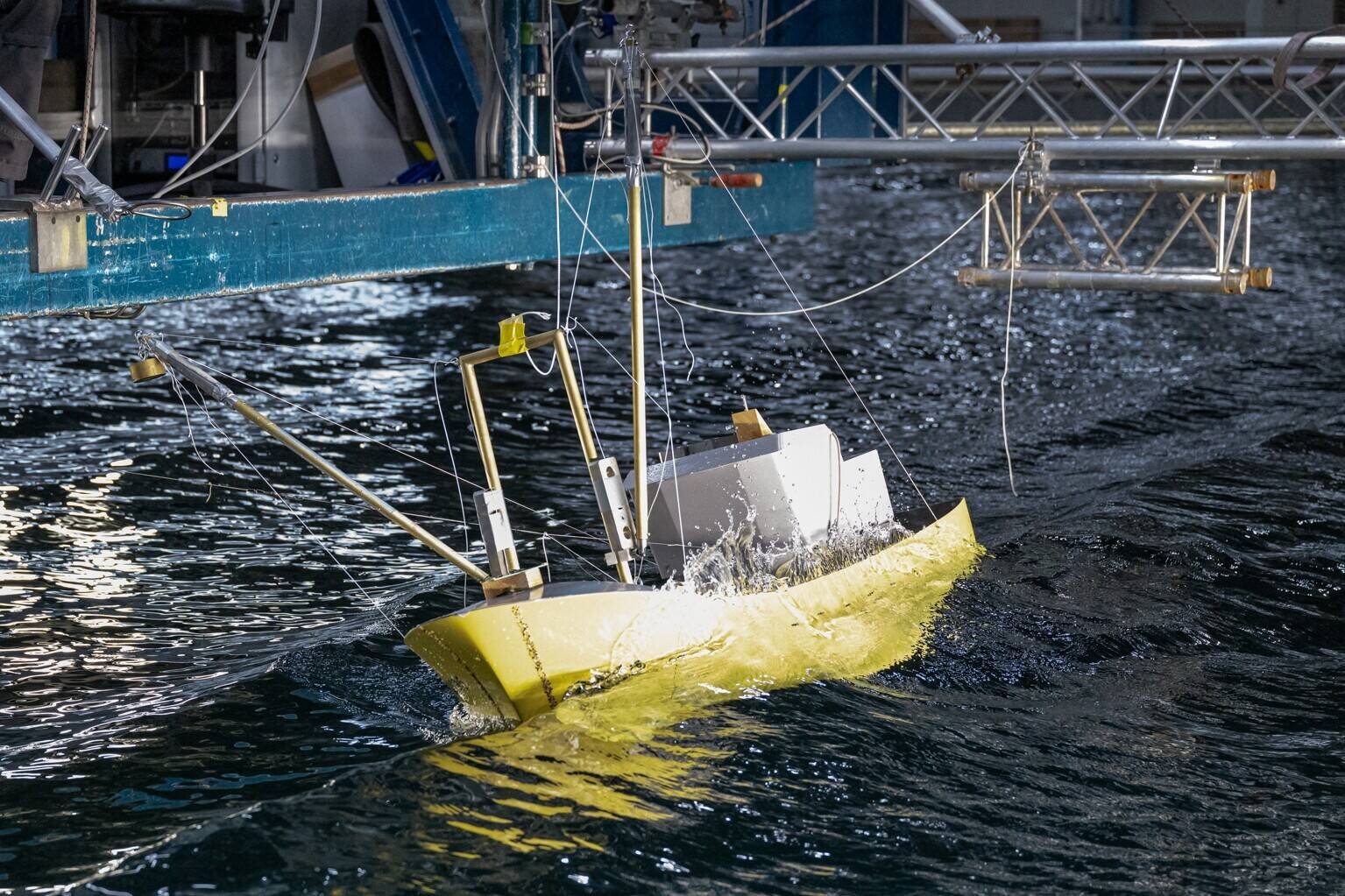
Beam trawler model in beam seas.
Micro MARIN Measurement System.
Interested? Contact us to discuss your options
The µMMS (Micro MARIN Measurement System) is specifically designed for light floaters, which means the measurement system is very light and small, such that it can easily be installed on a FOWT model.
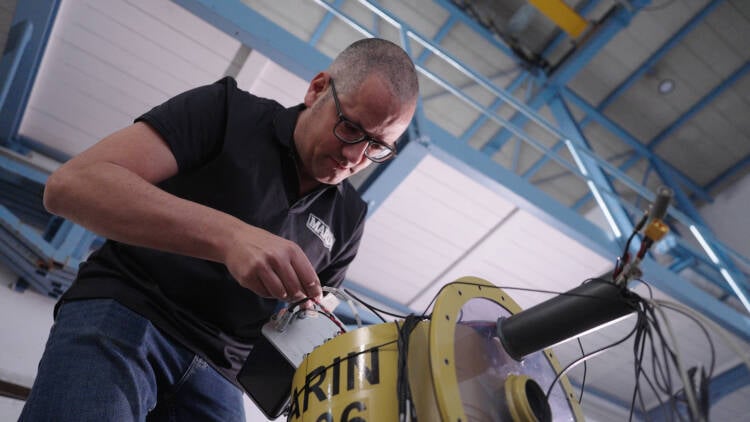
The µMMS is not only applicable for FOWT, but also for other small floaters and ships. The new measurement system makes it possible to accurately test small vessels, without the unwanted effect of the measurement cables.
For example, this year the Dutch Ministry of Infrastructure and Water Management contracted MARIN to investigate the dynamics that are involved in the capsizing of beam trawlers. The main goal of this project was to investigate the capsize risk in relation to fishing operations and the stability criteria.
Initially, we had planned to make a free sailing model for the tests that connects to the measurement system on the carriage. The combination of a small vessel and the high wave height in the tests resulted in a model weight of less than 100 kg. Given the small model size, low forces can have an impact on the rolling behaviour of the vessel. Therefore, to minimise the impact that the cables can have on the motions of the vessel, we minimised the number of sensors on board to the bare minimum. Additionally, we planned to use thinner cables than normal to reduce the weight even further.
The µMMS became available when we were designing the model. This offered the opportunity to make the model completely wireless and to measure more signals within the budget of the project. Without the measurement wires between the carriage and the model, the test setup was more versatile. No precautions were necessary to avoid interference from the measurement cables.
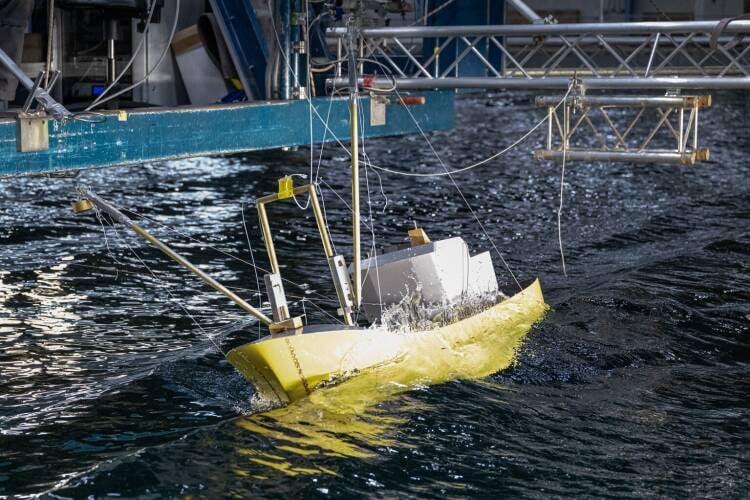
Beam trawler model in beam seas.
The new wireless measurement system µMMS used to test Hyundai Heavy Industries Hi-Float 15MW floating wind turbine in the Offshore basin.
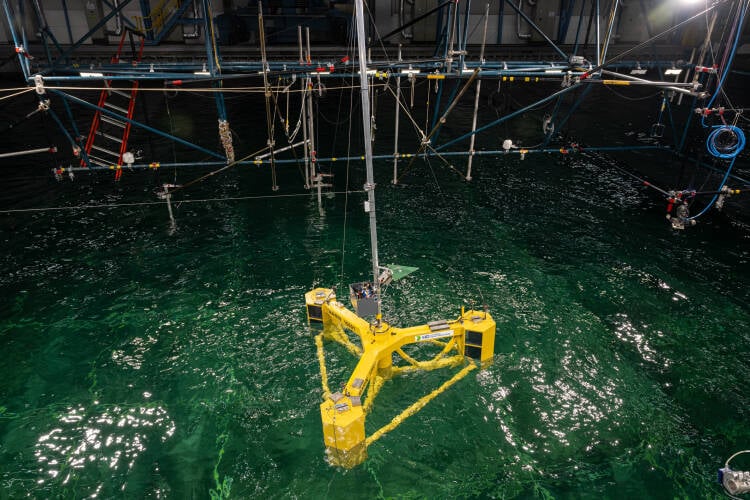
µMMS system available for clients
To mitigate this unwanted effect of the measurement cables, MARIN has developed a wireless measurement system called µMMS (Micro MARIN Measurement System). The system is specifically designed for light floaters, which means the measurement system is very light and small, such that it can easily be installed on a FOWT model. Furthermore, the system works on a battery pack and has real-time communication with the carriage so the basin crew can monitor the measurements during a model test.
The new wireless measurement system is now available for our clients, as well as a broad range of other comprehensive solutions for model testing floating turbines.
Micro MARIN Measurement System.
µMMS
(Micro MARIN Measurement System)
Universal analog sensor signal conditioning: Bridge, IEPE, Voltage
Local data storage or real-time streaming over ethernet (WiFi)
Programmable sampling rates & anti-alias filters
Irig time synchronisation (in sync with other MARIN systems)
Supports sensor ID for PnP
Dimensions: 15 x 12 x 17 cm
Weight: 1.3kg
Ingress protection: IP65
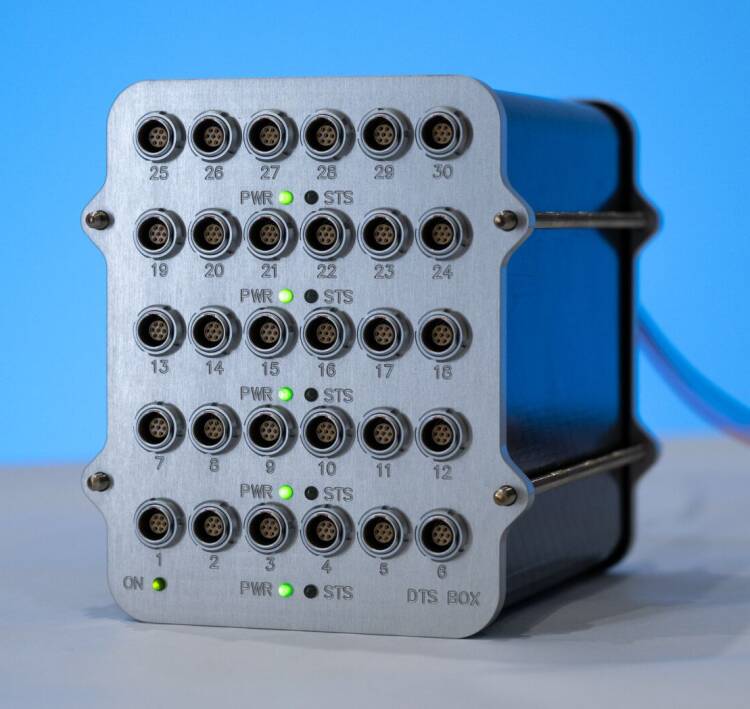
Increasing instrumentation
In the last decade we have seen that the amount of instrumentation on FOWT models has increased significantly, so we don’t merely measure motions and mooring line loads, but also additional signals such as impact loads, loads on the heave plate and internal loads. The growing amount of instrumentation on the models also has a significant downside, as the measurement cables are typically connected to the (earth fixed) carriage.
Especially for FOWT, this effect can be significant as these types of floaters are typically (very) light. Furthermore, it is difficult to quantify the effect of the cables on the dynamic floater motions and eigen periods. Although mitigating measures are taken by using light and flexible cables, the effect cannot be completely taken away.
October 2024, no. 141
A key point of model testing floating wind turbines is that wind and waves are presented simultaneously in the basin. This makes it possible to correctly study the complex motions and loads of the rotating turbine on a moving platform in wind and waves. For the first model tests with FOWT, no dedicated test setup was available, which resulted in using the existing test setup for oil & gas floaters.
However, over time, tailored model test techniques were developed specifically for model testing floating turbines. At first, these mainly focused on modelling the aerodynamic loading on the FOWT in the basin by developing high quality wind in the offshore basin, and different sizes of stock wind turbines. Alongside this, other aerodynamic modelling approaches were developed, whereby the loads are applied using either winches or small ducted fans as actuators controlled by aerodynamic BEM models.
MARIN has been involved in floating wind turbines (FOWT) right from the start, when the early pioneers started to develop the technology around 20 years ago. But in the last decade we have really seen the market getting more mature, shifting the projects from the concept to the design stage.
New wireless measurement setup for floating offshore wind turbines
Report
Create a MARIN account to stay updated
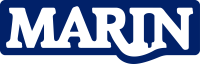