(Click image to enlarge)
The Zero Emssion Lab (ZEL) is a unique test facility worldwide for the research and testing of future marine propulsion and power systems, applying realistic, dynamic operating profiles.
Report
June 2023, no. 136
News
BlueWeek
AI Sail
TopTier
CFD
Zero Emission
Foil Design
Traffic studies
F-series
Manxman ferry
Cover
Two Dutch Research and Development Mobility (RDM) projects MENENS and SH2IPDRIVE are presented here.
Create a MARIN account to stay updated
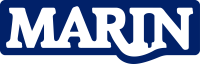
in the spotlight
Here we focus on zero-emission Research & Development and several Joint Industry Projects addressing the topic.
To reach zero-emission shipping a combination of measures are needed including energy efficiency measures such as hydrodynamic and operational improvements, use of renewable resources (wind and solar energy) and alternative fuels for power and energy systems.
Two trends dominate the requirements and designs of marine power systems. On the one hand, there are increasing restrictions on emissions of exhaust matter, radiation of exhaust heat and audible noise. And on the other hand, the power needs of payload, propulsion and auxiliary systems onboard maritime platforms are increasingly becoming electrified. Both trends are leading to integrated power and propulsion platforms that in some cases are supplied by new energy carriers like methanol, hydrogen or ammonia.
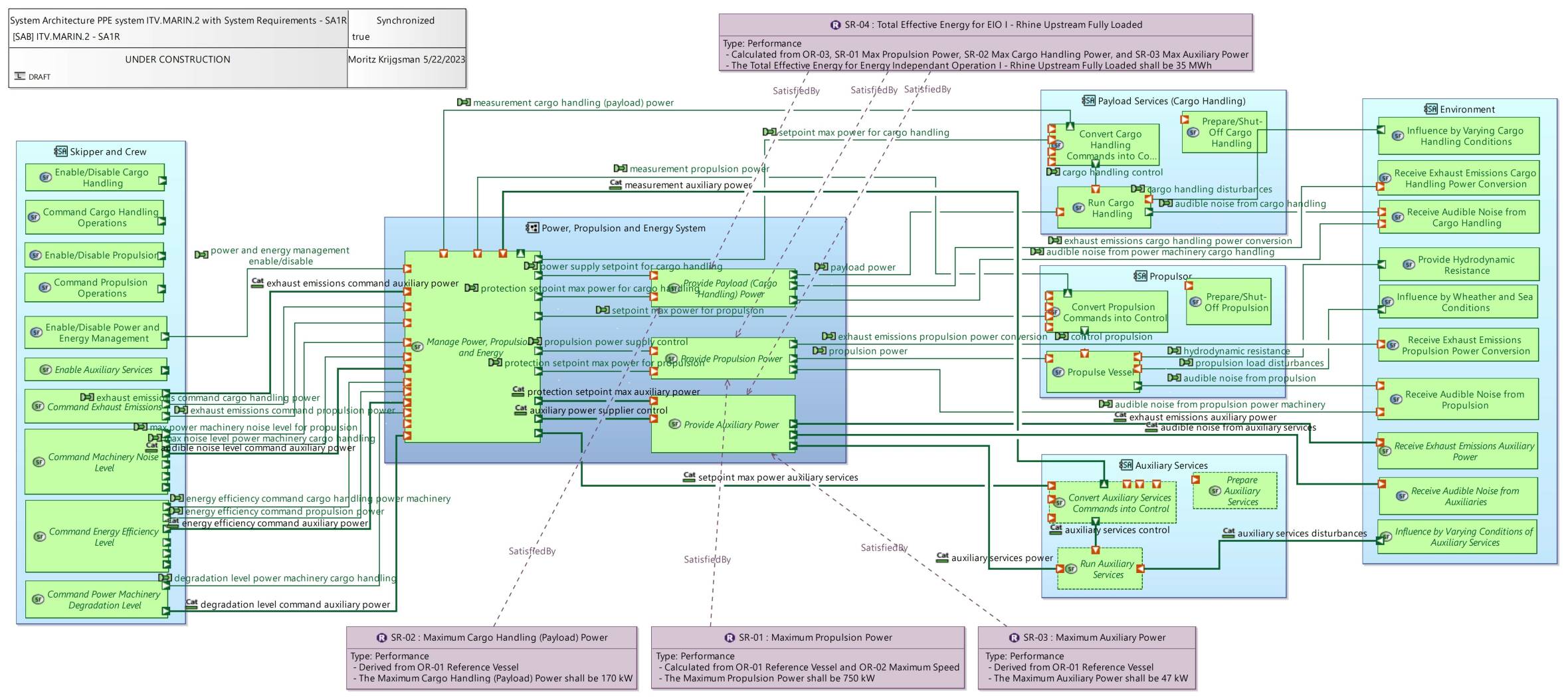
Figure1. System Architecture of the future Power, Propulsion and Energy System of an inland vessel with performance requirements.
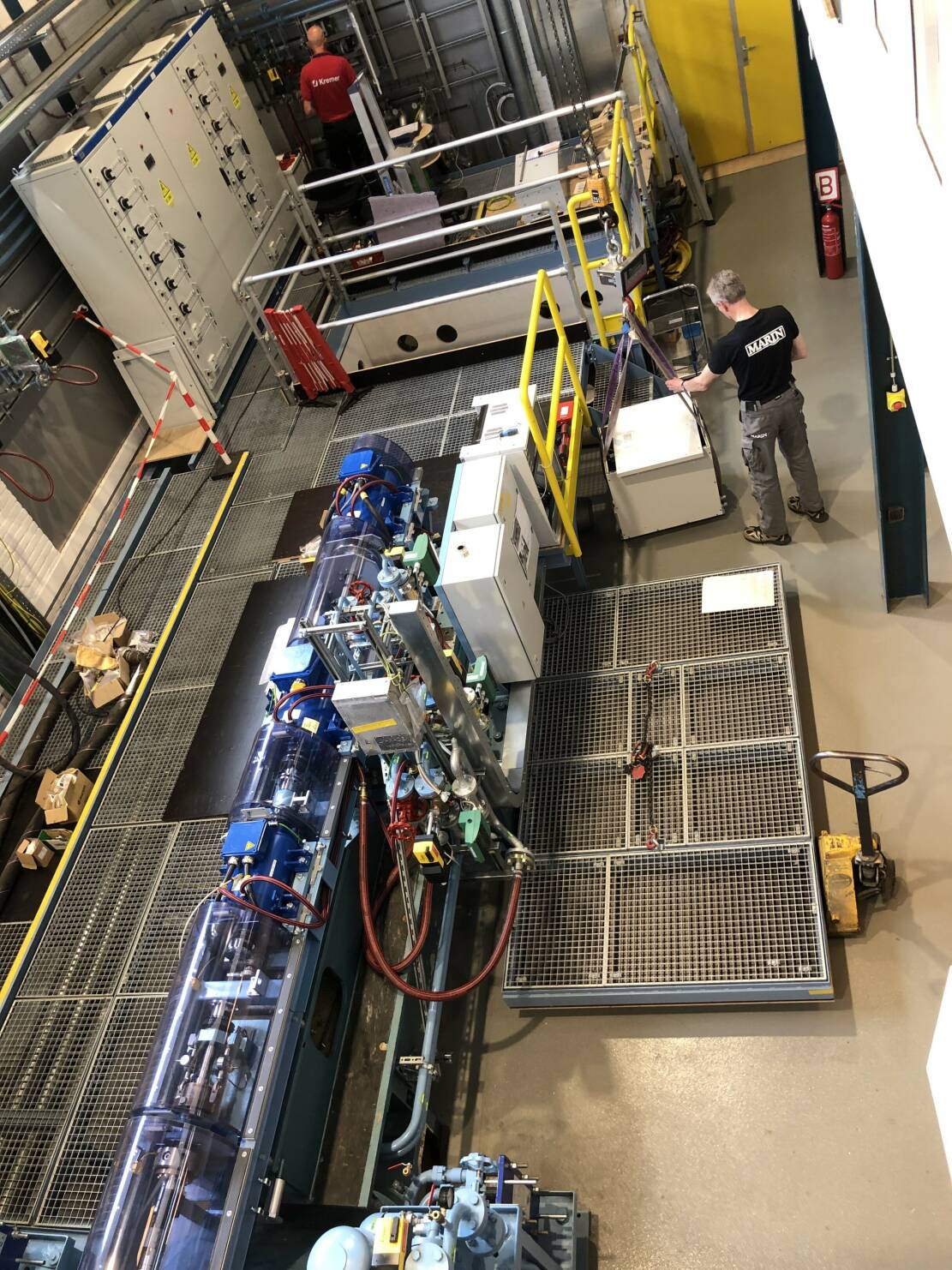
Zero Emission Lab under construction
The systematic way of approaching requirements and architectural design via MBSE provides the possibility of performing virtual and scaled physical model tests of PPE solutions. Those tests are done in the virtual and physical test environments of MARIN’s Zero Emission Lab (ZEL) and focus on the integration and interaction of components.
Besides system performances such as maximum power requirements, robustness, reliability, redundancy, human machine interfacing and maintainability can be assessed. By doing these tests before the engineering phase of a building project starts, all sorts of issues can be studied and dealt with in a relatively risk-free and inexpensive environment.
The test cases that have to be performed are assigned and formulated in the MBSE exploration and design layers. For example, if in the operational analysis a certain maximum vessel speed is specified, this can then be verified by a resistance test in one of the MARIN test basins. And if a maximum propulsion power is specified in the PPE System Architecture (ref. Figure 1), then the PPE performance can be tested in a scaled setup of the ZEL.
The virtual and physical Zero Emission Lab environments will be available in the second half of 2023.
Joint Industry Projects
MARIN works together with the sector on several topics - from explorative and conceptual design of power & energy systems, the simulation and testing of their performance, to the impact on the future fuel supply chain.
We do this in several Joint Industry Projects such as ZERO, Green Maritime Methanol, RDM MENENS and SH2IPDRIVE, which are briefly outlined below.
ZERO was launched in 2020. With 21 participants we are designing, building and testing the ‘engine rooms of the future’. The goal is to show new Power, Propulsion and Energy (PPE) systems which can operate reliably and still meet functional and emission requirements. In ZERO eight representative ships (use cases) are chosen and ship-specific emission reduction ambitions are defined. Following a Model Based System Engineering (MBSE) design methodology we defined operational requirements, explored possible PPE configurations and made conceptual designs of those PPE systems.
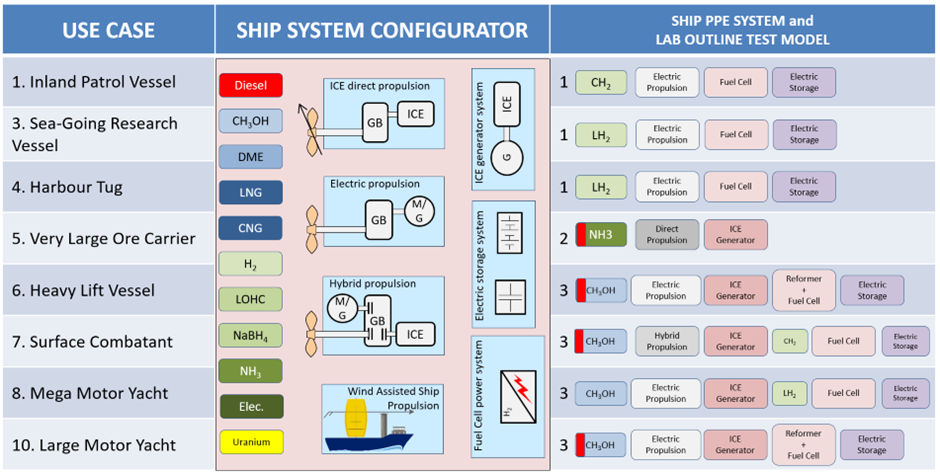
Figure 2. Overview of ships (use cases) in JIP ZERO (left) and the preferred solution (right) after the exploration phase. Note: Use cases 2 and 9 exist on paper but are not ‘activated’ in JIP ZERO.
For the exploration phase we used the sustainable power database for information such as energy densities, power densities, price levels, emission reduction potential etc. of the most important PPE system components. This database is not tailored for ZERO, but it is made for and with the sector. Figure 2 shows the impressive results of the exploration phase: a preferred PPE system configuration for every use case.
After exploration we made conceptual designs defining the main and supporting systems, sizes, weights and interconnections. Figure 3 shows a typical comparison of the PPE system volume distribution per use case. In the coming year these PPE designs will be configured in the ZEL and its virtual twin, v-ZEL, to verify and validate the performance of these systems.
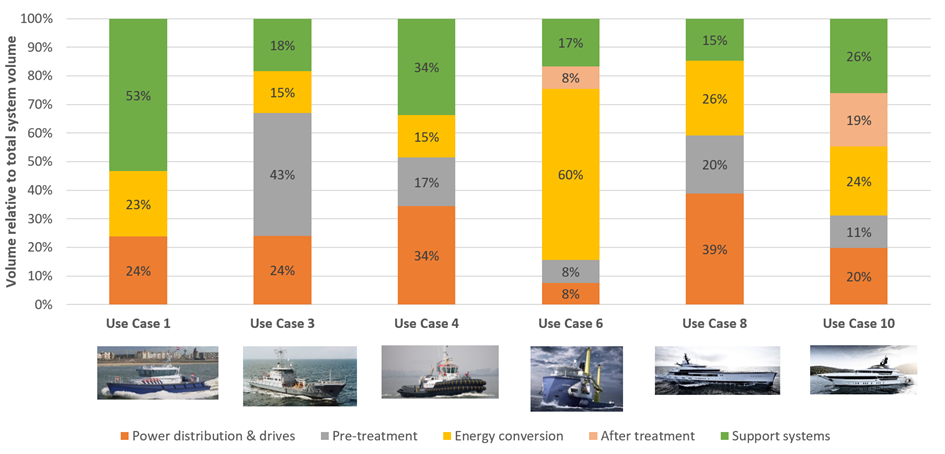
Figure 3. An overview of the power system volume (excluding energy carrier volume) for the seven of the eight use cases in JIP ZERO. The system configurations are as mentioned in Figure 3. Use Case 1: compressed hydrogen fuel cell electric propulsion. Use Case 3 and 4: liquid hydrogen fuel cell electric propulsion. Use Case 6: Methanol dual fuel ICE electric propulsion with fuel cells powered by methanol reforming.
Use Case 7: Methanol dual fuel ICE hybrid propulsion with compressed hydrogen powered fuel cells, Use Case 8: Methanol ICE electric propulsion with liquid hydrogen powered fuel cells. Use Case 10: Methanol dual fuel solution (through a combination of single fuel diesel and methanol ICEs) electric propulsion with fuel cells powered by methanol reforming.
Green Maritime Methanol (GMM) 1 and 2 is aiming to accelerate the uptake of green (synthetic) methanol and after the completion of GMM 2, plans are already underway for GMM 3. GMM 1 and 2 focus on the methanol supply chain, safety and the overall business case. An international consortium of more than 30 partners are involved in the project.
Methanol as an Energy Step towards Zero-Emission Dutch Shipping (MENENS) aims to accelerate the uptake of methanol. The 21 partners represent the Dutch maritime sector right across the board, from fleet owners to ship designers, from shipyards to suppliers. There is a wide-ranging research focus, which encompasses the in-depth knowledge development of methanol power generation, storage safety, system design & integration, and lab testing including power & energy management and control to retrofits, full-scale measurements and validation feedback. Use cases (mega yacht, navy research/supply vessel, offshore working vessel) are defined to look beyond the horizon and envision the ships of the future. MARIN is active in most of the work packages and brings its expertise on PPE system design, integration and validation to the project.
SH2IPDRIVE consists of 25 companies and research institutions with the objective of accelerating the introduction of H2-based systems in the marine industry by designing reliable, safe and cost-effective solutions. MARIN is involved in several work packages related to data collection and validation, PPE system design, modelling and integration, and safety.
For the (concept) design of zero-emission PPE systems which only have limited installed power sometimes, high fidelity operational power profiles are needed. Figure 4 shows a typical load profile of the shaft generator in relation to where the ship is located at the time. This gives a general idea of the load during a voyage. Together with the monitoring of large power fluctuations in specific conditions, this can be used in the validation (testing) phase of the newly designed hydrogen-based PPE systems.
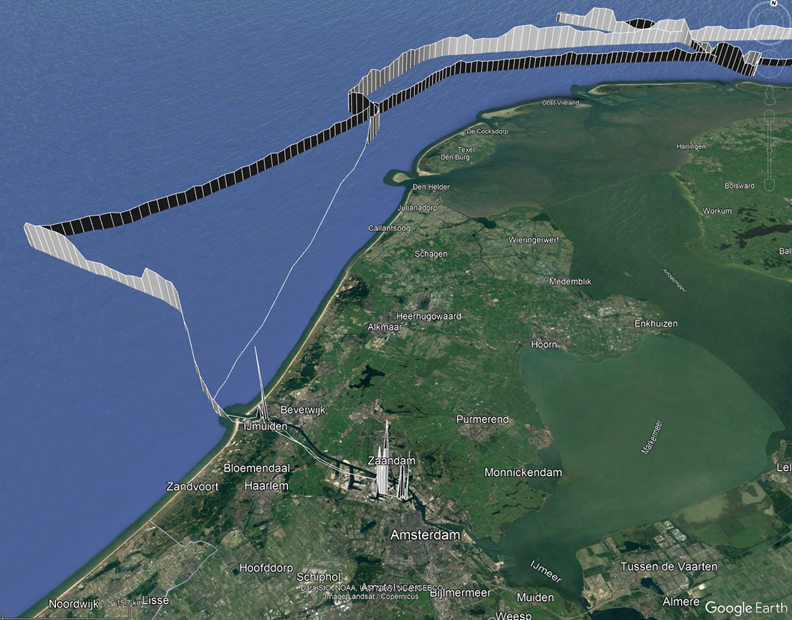
Figure 4. Route of a general cargo ship near the Dutch Coast. The Z axis of the plotted trajectory corresponds to the shaft generator power level, giving insight into the use of power during the voyage.
More info:
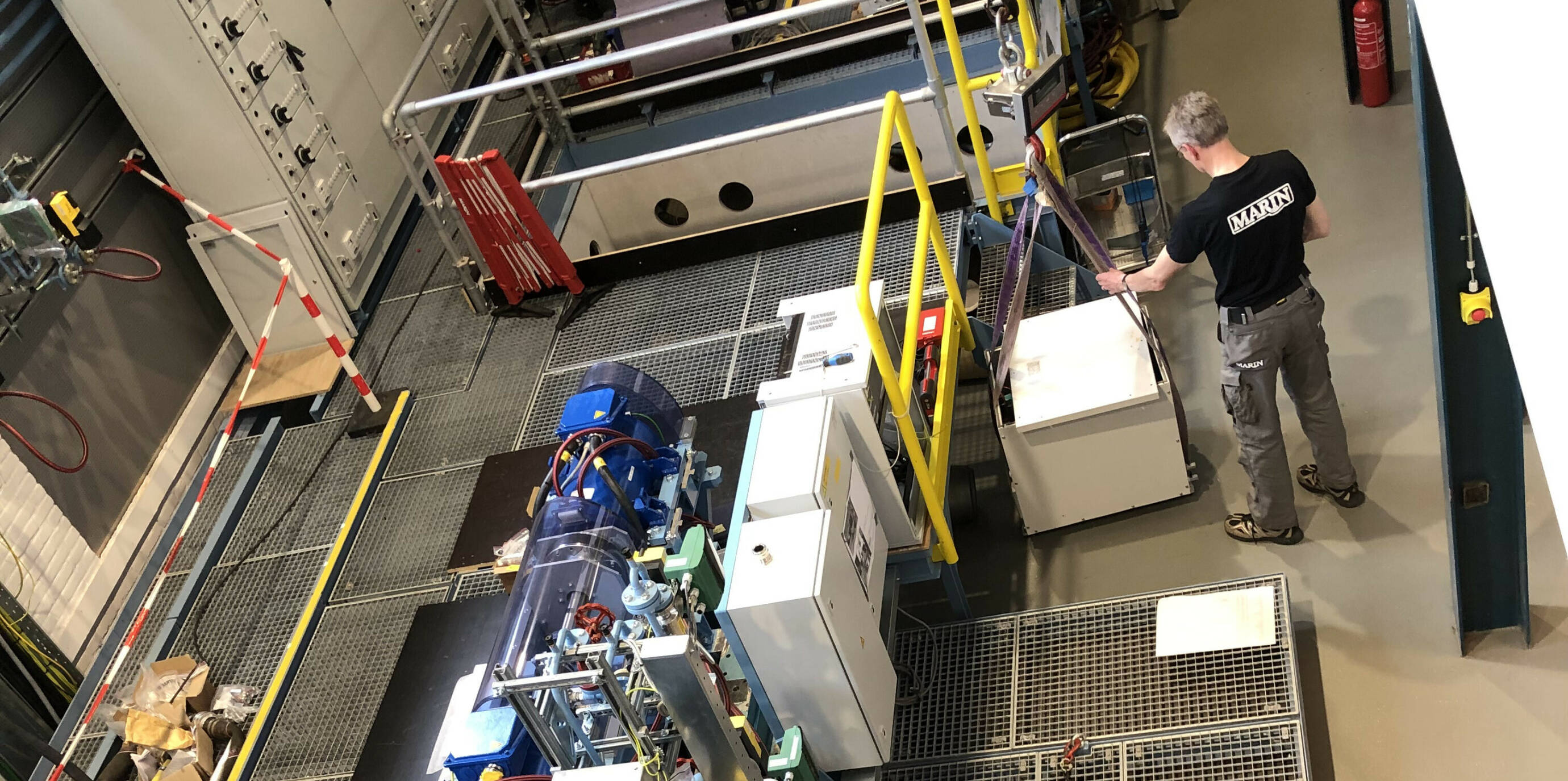
More info:
The Zero Emssion Lab (ZEL) is a unique test facility worldwide for the research and testing of future marine propulsion and power systems, applying realistic, dynamic operating profiles.
SH2IPDRIVE consists of 25 companies and research institutions with the objective of accelerating the introduction of H2-based systems in the marine industry by designing reliable, safe and cost-effective solutions. MARIN is involved in several work packages related to data collection and validation, PPE system design, modelling and integration, and safety.
For the (concept) design of zero-emission PPE systems which only have limited installed power sometimes, high fidelity operational power profiles are needed. Figure 4 shows a typical load profile of the shaft generator in relation to where the ship is located at the time. This gives a general idea of the load during a voyage. Together with the monitoring of large power fluctuations in specific conditions, this can be used in the validation (testing) phase of the newly designed hydrogen-based PPE systems.
Methanol as an Energy Step towards Zero-Emission Dutch Shipping (MENENS) aims to accelerate the uptake of methanol. The 21 partners represent the Dutch maritime sector right across the board, from fleet owners to ship designers, from shipyards to suppliers. There is a wide-ranging research focus, which encompasses the in-depth knowledge development of methanol power generation, storage safety, system design & integration, and lab testing including power & energy management and control to retrofits, full-scale measurements and validation feedback. Use cases (mega yacht, navy research/supply vessel, offshore working vessel) are defined to look beyond the horizon and envision the ships of the future. MARIN is active in most of the work packages and brings its expertise on PPE system design, integration and validation to the project.
Two Dutch Research and Development Mobility (RDM) projects MENENS and SH2IPDRIVE are presented here.
Green Maritime Methanol (GMM) 1 and 2 is aiming to accelerate the uptake of green (synthetic) methanol and after the completion of GMM 2, plans are already underway for GMM 3. GMM 1 and 2 focus on the methanol supply chain, safety and the overall business case. An international consortium of more than 30 partners are involved in the project.
Figure 3. An overview of the power system volume (excluding energy carrier volume) for the seven of the eight use cases in JIP ZERO. The system configurations are as mentioned in Figure 3. Use Case 1: compressed hydrogen fuel cell electric propulsion. Use Case 3 and 4: liquid hydrogen fuel cell electric propulsion. Use Case 6: Methanol dual fuel ICE electric propulsion with fuel cells powered by methanol reforming.
Use Case 7: Methanol dual fuel ICE hybrid propulsion with compressed hydrogen powered fuel cells, Use Case 8: Methanol ICE electric propulsion with liquid hydrogen powered fuel cells. Use Case 10: Methanol dual fuel solution (through a combination of single fuel diesel and methanol ICEs) electric propulsion with fuel cells powered by methanol reforming.
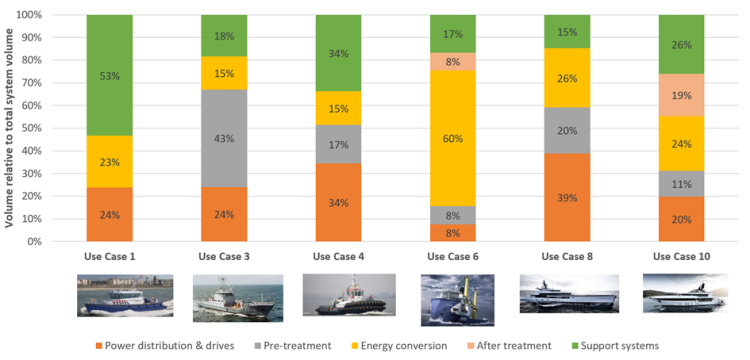
For the exploration phase we used the sustainable power database for information such as energy densities, power densities, price levels, emission reduction potential etc. of the most important PPE system components. This database is not tailored for ZERO, but it is made for and with the sector. Figure 2 shows the impressive results of the exploration phase: a preferred PPE system configuration for every use case.
After exploration we made conceptual designs defining the main and supporting systems, sizes, weights and interconnections. Figure 3 shows a typical comparison of the PPE system volume distribution per use case. In the coming year these PPE designs will be configured in the ZEL and its virtual twin, v-ZEL, to verify and validate the performance of these systems.
Figure 2. Overview of ships (use cases) in JIP ZERO (left) and the preferred solution (right) after the exploration phase. Note: Use cases 2 and 9 exist on paper but are not ‘activated’ in JIP ZERO.
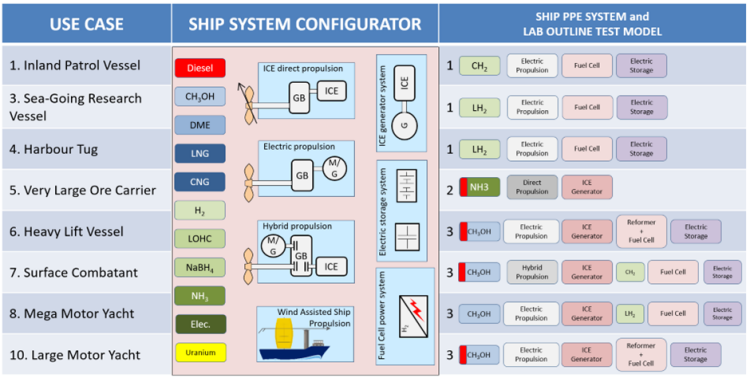
ZERO was launched in 2020. With 21 participants we are designing, building and testing the ‘engine rooms of the future’. The goal is to show new Power, Propulsion and Energy (PPE) systems which can operate reliably and still meet functional and emission requirements. In ZERO eight representative ships (use cases) are chosen and ship-specific emission reduction ambitions are defined. Following a Model Based System Engineering (MBSE) design methodology we defined operational requirements, explored possible PPE configurations and made conceptual designs of those PPE systems.
We do this in several Joint Industry Projects such as ZERO, Green Maritime Methanol, RDM MENENS and SH2IPDRIVE, which are briefly outlined below.
MARIN works together with the sector on several topics - from explorative and conceptual design of power & energy systems, the simulation and testing of their performance, to the impact on the future fuel supply chain.
Joint Industry Projects
Figure 4. Route of a general cargo ship near the Dutch Coast. The Z axis of the plotted trajectory corresponds to the shaft generator power level, giving insight into the use of power during the voyage.
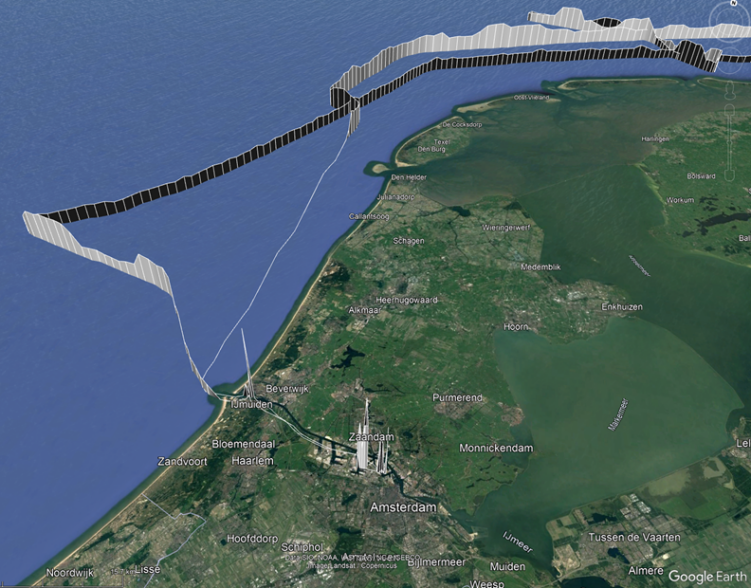
The systematic way of approaching requirements and architectural design via MBSE provides the possibility of performing virtual and scaled physical model tests of PPE solutions. Those tests are done in the virtual and physical test environments of MARIN’s Zero Emission Lab (ZEL) and focus on the integration and interaction of components.
Besides system performances such as maximum power requirements, robustness, reliability, redundancy, human machine interfacing and maintainability can be assessed. By doing these tests before the engineering phase of a building project starts, all sorts of issues can be studied and dealt with in a relatively risk-free and inexpensive environment.
The test cases that have to be performed are assigned and formulated in the MBSE exploration and design layers. For example, if in the operational analysis a certain maximum vessel speed is specified, this can then be verified by a resistance test in one of the MARIN test basins. And if a maximum propulsion power is specified in the PPE System Architecture (ref. Figure 1), then the PPE performance can be tested in a scaled setup of the ZEL.
The virtual and physical Zero Emission Lab environments will be available in the second half of 2023.
Zero Emission Lab under construction
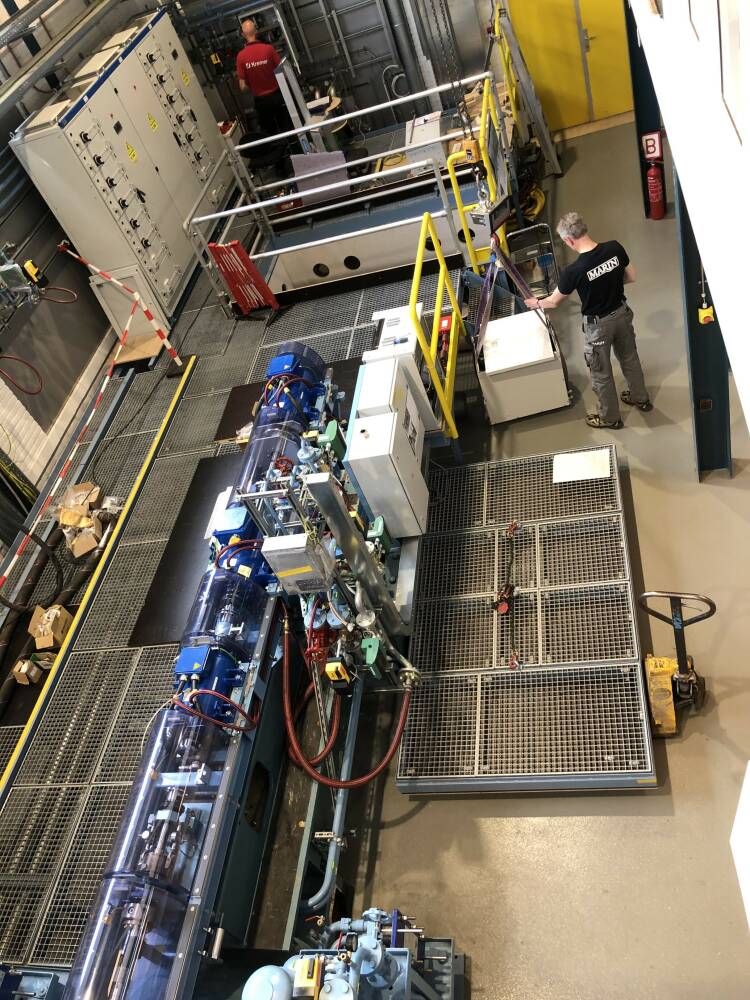
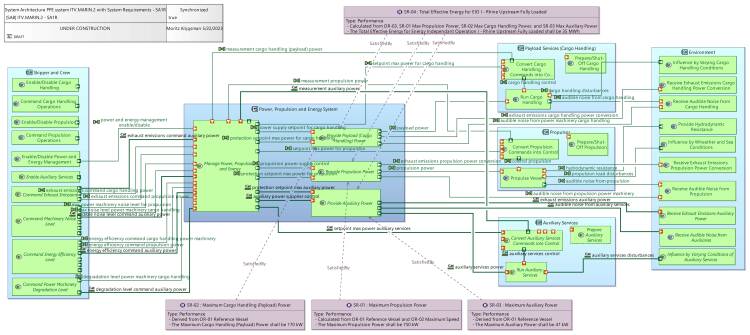
(Click image to enlarge)
Figure1. System Architecture of the future Power, Propulsion and Energy System of an inland vessel with performance requirements.
Report
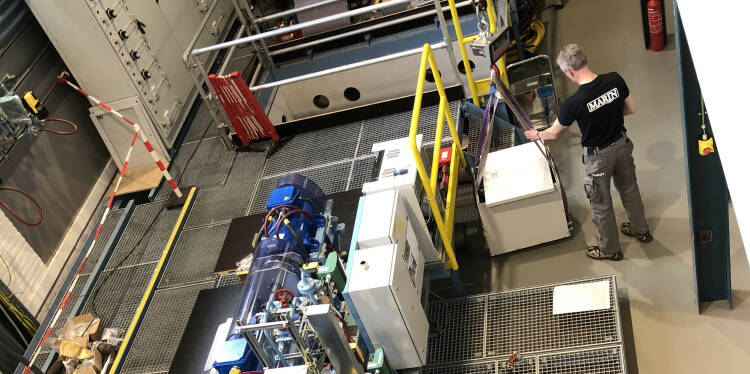
To reach zero-emission shipping a combination of measures are needed including energy efficiency measures such as hydrodynamic and operational improvements, use of renewable resources (wind and solar energy) and alternative fuels for power and energy systems.
Two trends dominate the requirements and designs of marine power systems. On the one hand, there are increasing restrictions on emissions of exhaust matter, radiation of exhaust heat and audible noise. And on the other hand, the power needs of payload, propulsion and auxiliary systems onboard maritime platforms are increasingly becoming electrified. Both trends are leading to integrated power and propulsion platforms that in some cases are supplied by new energy carriers like methanol, hydrogen or ammonia.
June 2023, no. 136
Here we focus on zero-emission Research & Development and several Joint Industry Projects addressing the topic.
in the spotlight
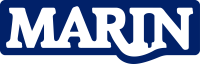