References:
B. Jürgens (2002) “The Fascination of the Voith-Schneider Propeller – History and Engineering”, published by Koehlers Verlagsgesellschaft mbH, Hamburg, ISBN 3-7822-0859-5.
J.D. van Manen (1966), "Results of Systematic Tests with Vertical Axis Propellers", International Shipbuilding Progress, Vol. 13, No. 148, pp. 382-398.
J.D. van Manen and T. van Terwisga (1996), "A New Way of Simulating Whale Tail Propulsion", 21stONR Symposium on Naval Hydrodynamics, Trondheim.
J.G. Vermeiden, K. Kooiker, F.H. Lafeber, T. van Terwisga, B. Cerup-Simonsen and R. Folsø (2012) “A Systematic Experimental Study on Powering Performance of Flapping Foil Propulsors”, 29thONR Symposium on Naval Hydrodynamics, Gothenburg.
B. Goris (2012), “O-Foil Propulsion Concept Successfully Tested”, SWZ|Maritime News, December 10.
Janne Pohjalainen (ABB, Global Product Line Manager) and Jie Dang (MARIN).
Create a MARIN account to stay updated
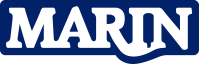
Report
June 2025, no. 144
Interested? Contact us to discuss your options
Potential mainstream marine propulsion solutions
To validate the ABB DynafinTM, MARIN developed an open water test setup and used a six-component balance to measure the thrust and side force. In addition, a shaft torque transducer and an encoder were inserted between the main electric motor and the orbital disc. All fin servos were also calibrated with a six-component shaft force transducer at all rotation rates, for positive and negative torques. In this way, the thrust, the main shaft torque and the fin torques (including fin power regeneration) were all measured and the hydrodynamic open-water efficiency was determined. By tripping turbulent flow on the fin surfaces and extrapolating results to full scale using section profile theories, MARIN predicted an open-water efficiency of ABB DynafinTMexceeding 80%.
With ABB’s proven track record of electric drive systems, such as the podded propulsors operating successfully in harsh, open and icy waters with high reliability and durability, ABB DynafinTMmay overcome the mechanical issues faced by the other inventions for decades with optimised trochoidal blade motions. This innovation could make a transition for the fin propulsion from the present niche products to mainstream marine propulsion solutions, offering high efficiency, reduced fuel consumption, and lower emissions.
Figure 3. ABB DynafinTM scale model in the MARIN Concept Basin (2025).
Fin propulsion revival
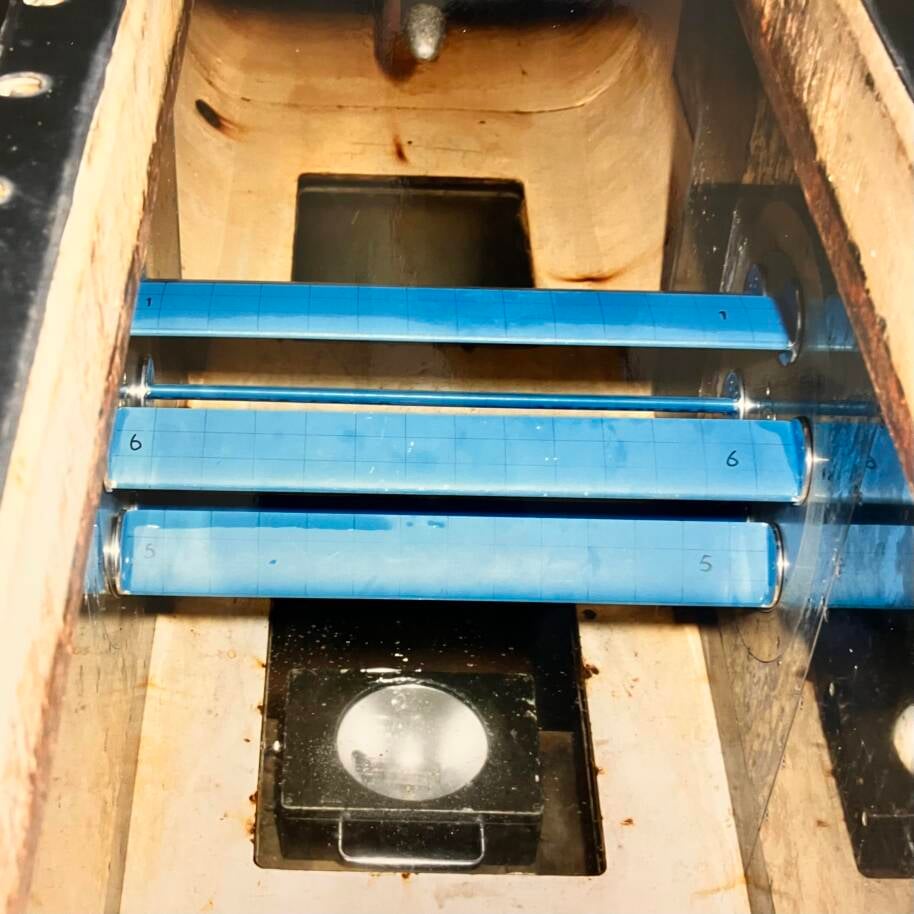
Figure 2. A Whale Tail Wheel (TWT) scale model in MARIN’s cavitation tunnel (1996).
From left to right: Jiangwei Huang, Bin Liu, David Petersson, Tomas Botold, Peter Fransson, Michel Veenendaal and René Bosman.
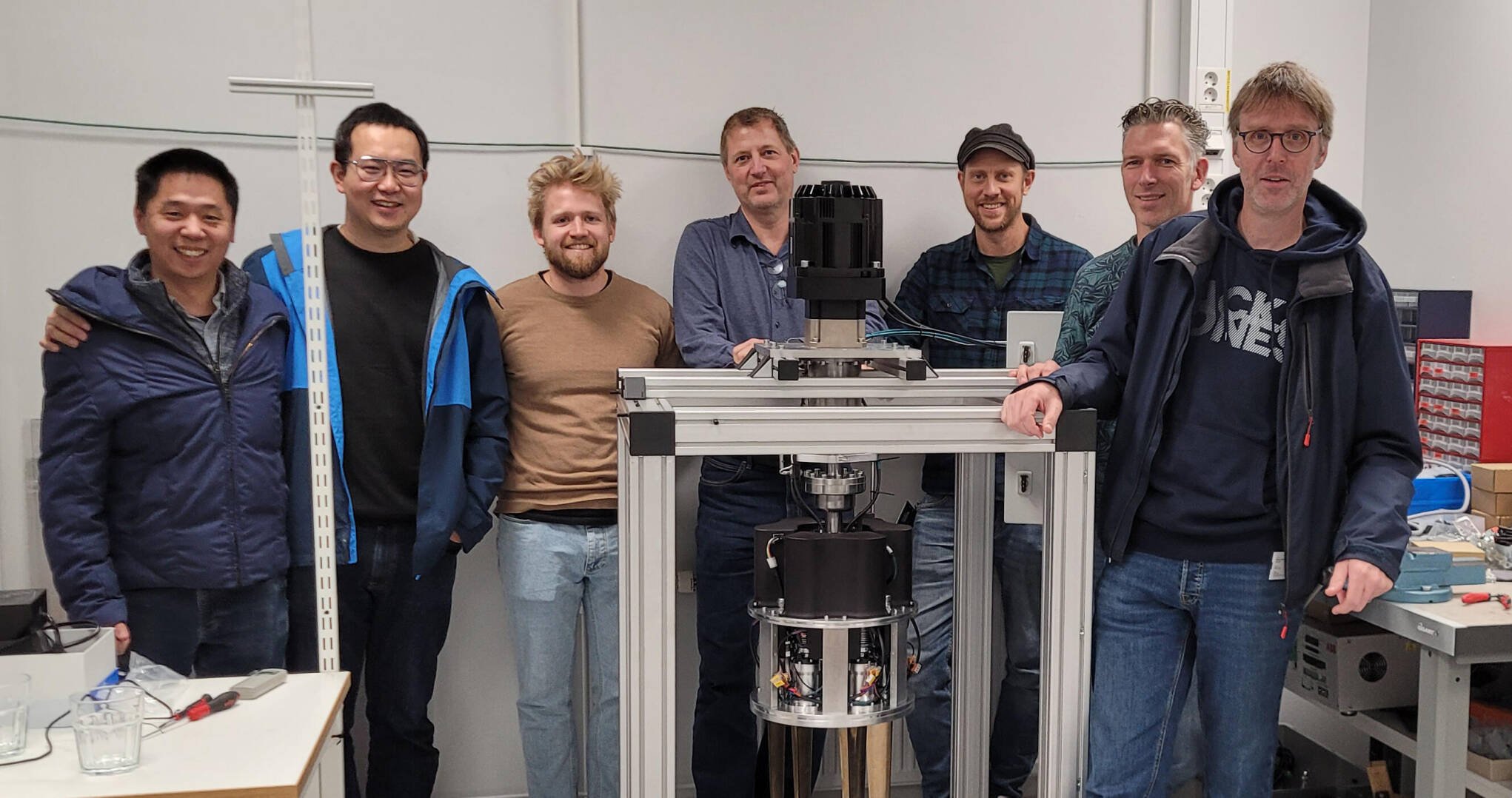
René Bosman
Senior Specialist Mechanical Measurement, MARIN
Jie Dang
Senior Project Manager, MARIN
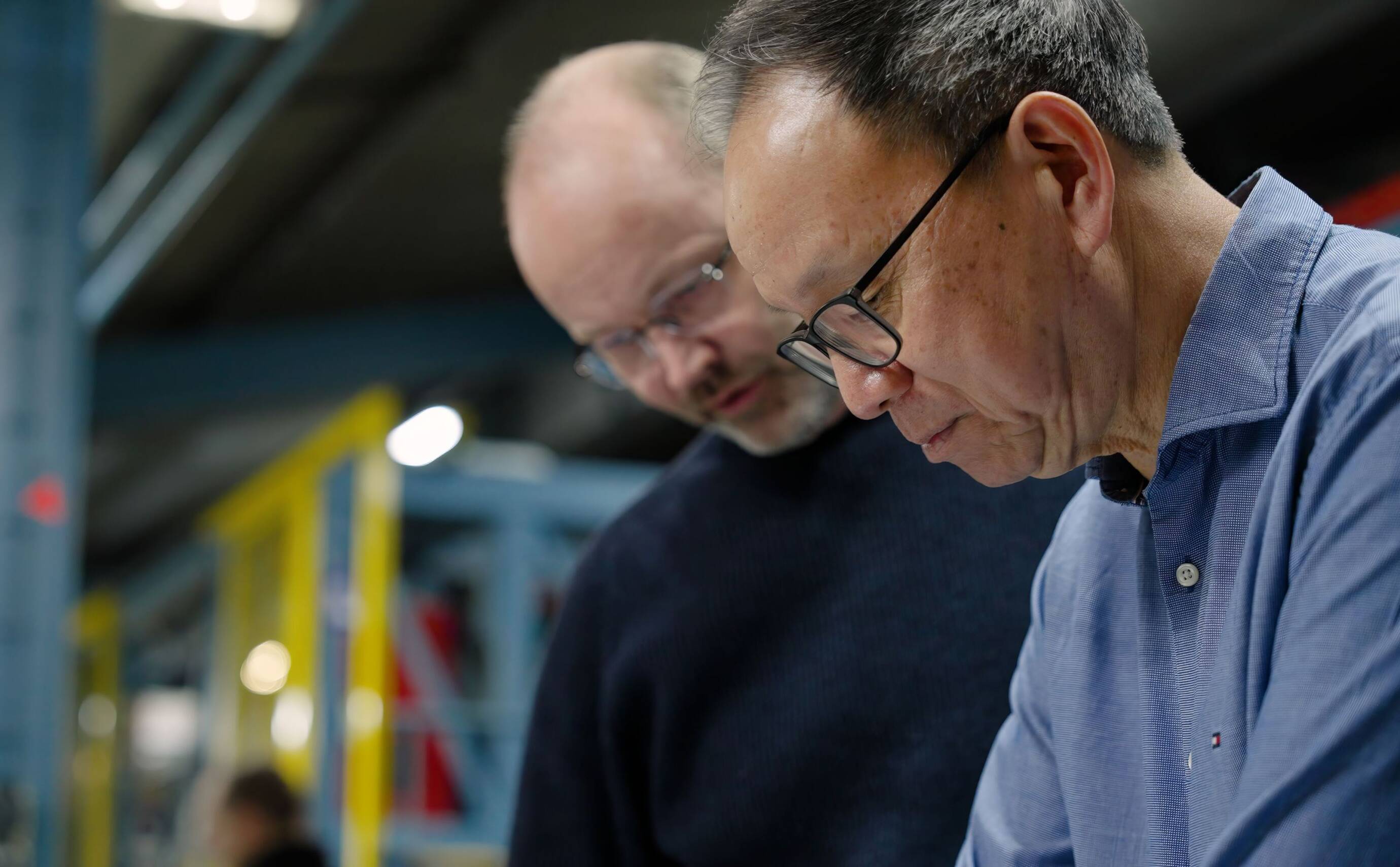
Better Ships, Blue Oceans
More info
www.marin.nl/sosc
October 2024, no. 142
In the past decades, more fin propulsion systems have been proposed by both small startups and big cooperations to mimic the swimming of a fish. Many of them were tested at MARIN, including orbital and linear motion designs. Examples with linear motions include the vertical FinProp (Vermeiden et al. 2012) and the O-foil with a single, large horizontal fin (Goris, 2012). Both rigid and flexible fin blades were investigated, achieving open-water efficiencies exceeding 90%, however only at very low thrust loading coefficients.
Obstacles to industrial applications
Although balancing high efficiency with sufficient thrust for practical use remains challenging, as these goals often conflict, the primary obstacle to achieve industrial applications has been reliability and durability. Despite successful prototypes and full-scale trials, mechanical failures have hindered progress. Even the optimised motions, following the Sparenberg’s optimum criterion that deviates from the standard cycloidal motion, proved difficult to implement, relegating those inventions to academic studies for decades. So far, only the VSPs have an impressive successful operation record, although this is limited to standard epi-cycloidal blade motions with a low pitch.
Amidst the ongoing electrification of marine propulsion systems in the present energy transition, fin propulsion is experiencing a revival, mainly due to its high propulsive efficiency. In February, MARIN tested a new system called ABB DynafinTM (Figure 3). In this system, each fin is driven by an individual electric motor. This gives full freedom of the fin motions, enabling precise control over epi-cycloidal and trochoidal motions at any pitch setting. Supported by RANS CFD calculations and motion optimisation, and with ABB’s robotic control technology, the fins can follow the optimised trajectories for maximum efficiency, enhanced manoeuvring, high precision dynamic positioning, better cavitation control, and roll damping of the ship in rough seas.
Whale Tail Wheel
Inspired by these early studies, the Whale Tail Wheel (WTW) propulsion system was developed later at MARIN (Figure 2). Instead of vertical fins, this system consisted of horizontally placed fins spanning up to the ship’s width, rotating via orbit discs and following optimised trochoidal motions (Van Manen and Van Terwisga 1996). With its large propulsion area and low thrust loading, combined with low rotation rates to reduce viscous losses, the WTW achieved an impressive 84% open-water efficiency. Subsequent studies confirmed that it had better cavitation performance, noting that low thrust loading also minimised cavitation risks and enhanced practical applicability.
This required higher pitch angles in the slipstream coming from the first half of a cycle. These early tests explored not only low-pitch epi-cycloidal fin motions (e < 1, P/D < π, circumferential velocity > advance velocity) such as the VSPs, but also high-pitch trochoidal motions (e > 1, P/D > π, circumferential velocity < advance velocity). These model tests already demonstrated high open-water efficiencies up to 70% for trochoidal motions.
First systematic tests in 1963
MARIN, then known as the Netherlands Ship Model Basin (NSMB), performed the first systematic tests on vertical fin propulsors in 1963 (Figure 1), featuring various fin blades and motions (Van Manen 1966). In addition to a standard cycloidal motion, governed by an eccentricity-radius ratio ‘e’ of all fin normals, significant improvements were found by applying a so-called Sparenberg’s optimum criterion, which maintained constant bound circulation on the fins to minimise energy losses by preventing transverse vortex shedding.
Vertical fin propulsors have been in operation since June 1931 when the first Voith Schneider Propulsor (VSP) was fitted to a ship (Jürgens 2002). Renowned for their superior manoeuvrability and roll-damping capabilities, VSPs were deployed widely over the years. And recently they have attracted attention again. Interest in fin propulsion has resurged, but this time with a focus on achieving exceptionally high efficiency through optimised fin motions.
Fin propulsion is experiencing a revival due to its high propulsive efficiency. In early 2025, MARIN successfully tested a new fully electric system – an ABB DynafinTM.
Figure 1. Test equipment for vertical axis propellers in a cavitation tunnel at NSMB (1963).
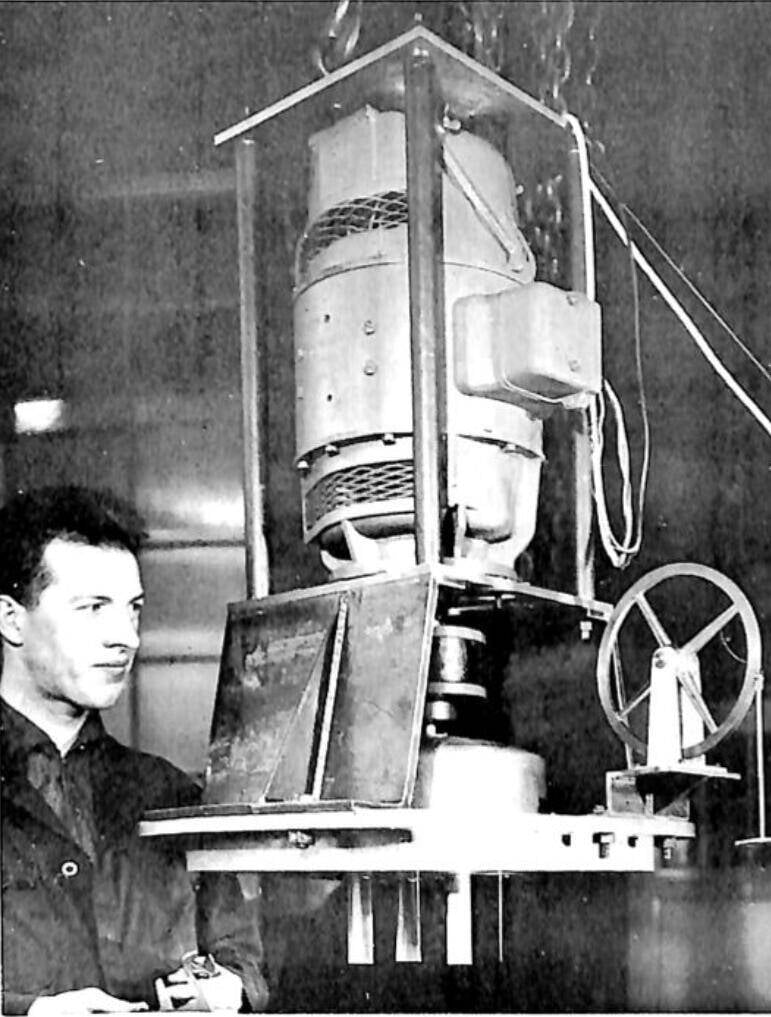
Potential mainstream marine propulsion solutions
To validate the ABB DynafinTM, MARIN developed an open water test setup and used a six-component balance to measure the thrust and side force. In addition, a shaft torque transducer and an encoder were inserted between the main electric motor and the orbital disc. All fin servos were also calibrated with a six-component shaft force transducer at all rotation rates, for positive and negative torques. In this way, the thrust, the main shaft torque and the fin torques (including fin power regeneration) were all measured and the hydrodynamic open-water efficiency was determined. By tripping turbulent flow on the fin surfaces and extrapolating results to full scale using section profile theories, MARIN predicted an open-water efficiency of ABB DynafinTMexceeding 80%.
With ABB’s proven track record of electric drive systems, such as the podded propulsors operating successfully in harsh, open and icy waters with high reliability and durability, ABB DynafinTMmay overcome the mechanical issues faced by the other inventions for decades with optimised trochoidal blade motions. This innovation could make a transition for the fin propulsion from the present niche products to mainstream marine propulsion solutions, offering high efficiency, reduced fuel consumption, and lower emissions.
Figure 3. ABB DynafinTM scale model in the MARIN Concept Basin (2025).
In the past decades, more fin propulsion systems have been proposed by both small startups and big cooperations to mimic the swimming of a fish. Many of them were tested at MARIN, including orbital and linear motion designs. Examples with linear motions include the vertical FinProp (Vermeiden et al. 2012) and the O-foil with a single, large horizontal fin (Goris, 2012). Both rigid and flexible fin blades were investigated, achieving open-water efficiencies exceeding 90%, however only at very low thrust loading coefficients.
Obstacles to industrial applications
Although balancing high efficiency with sufficient thrust for practical use remains challenging, as these goals often conflict, the primary obstacle to achieve industrial applications has been reliability and durability. Despite successful prototypes and full-scale trials, mechanical failures have hindered progress. Even the optimised motions, following the Sparenberg’s optimum criterion that deviates from the standard cycloidal motion, proved difficult to implement, relegating those inventions to academic studies for decades. So far, only the VSPs have an impressive successful operation record, although this is limited to standard epi-cycloidal blade motions with a low pitch.
Amidst the ongoing electrification of marine propulsion systems in the present energy transition, fin propulsion is experiencing a revival, mainly due to its high propulsive efficiency. In February, MARIN tested a new system called ABB DynafinTM (Figure 3). In this system, each fin is driven by an individual electric motor. This gives full freedom of the fin motions, enabling precise control over epi-cycloidal and trochoidal motions at any pitch setting. Supported by RANS CFD calculations and motion optimisation, and with ABB’s robotic control technology, the fins can follow the optimised trajectories for maximum efficiency, enhanced manoeuvring, high precision dynamic positioning, better cavitation control, and roll damping of the ship in rough seas.
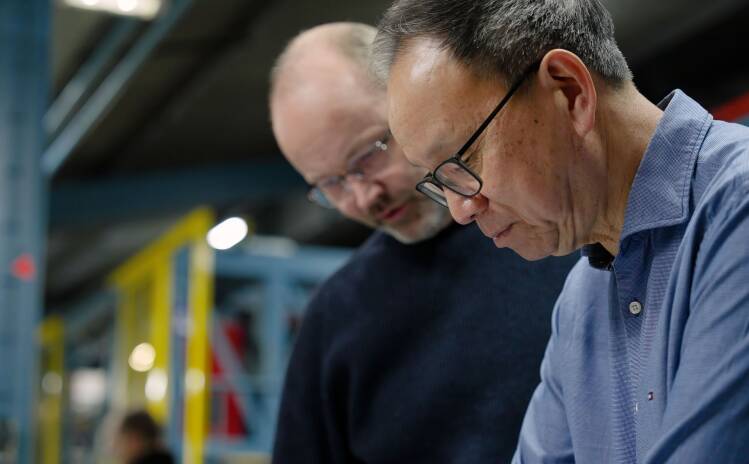
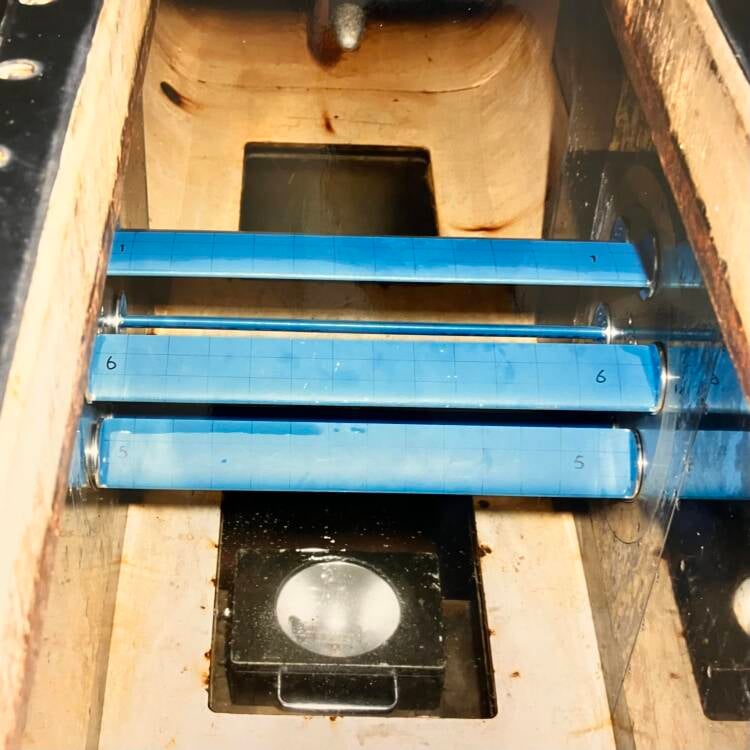
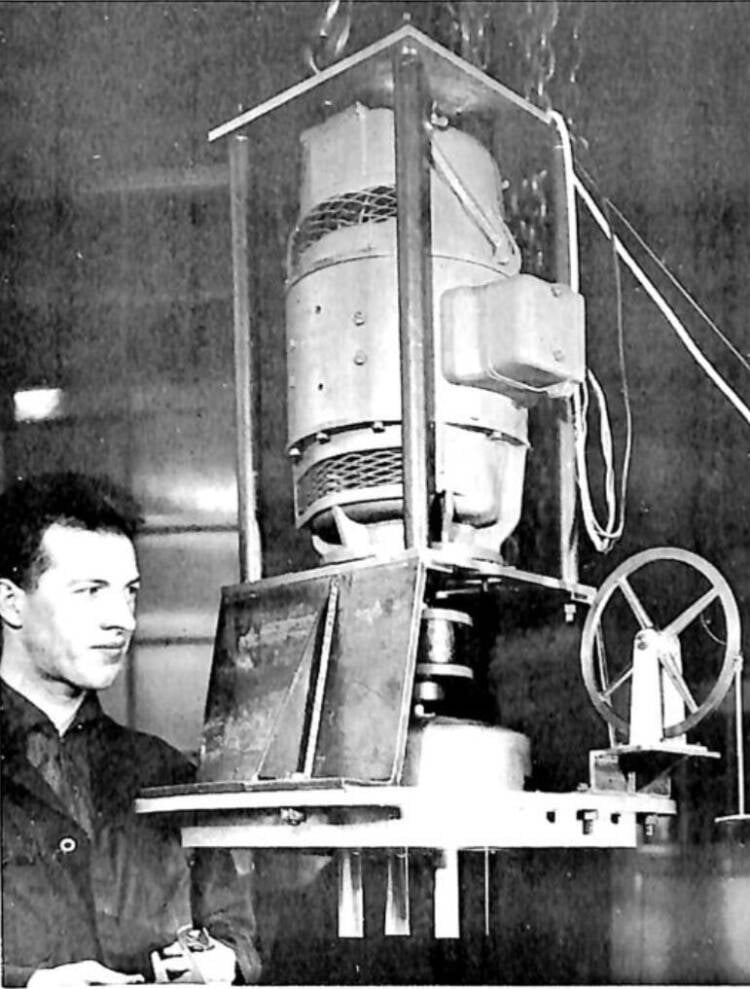
Report
Interested? Contact us to discuss your options
From left to right: Jiangwei Huang, Bin Liu, David Petersson, Tomas Botold, Peter Fransson, Michel Veenendaal and René Bosman.
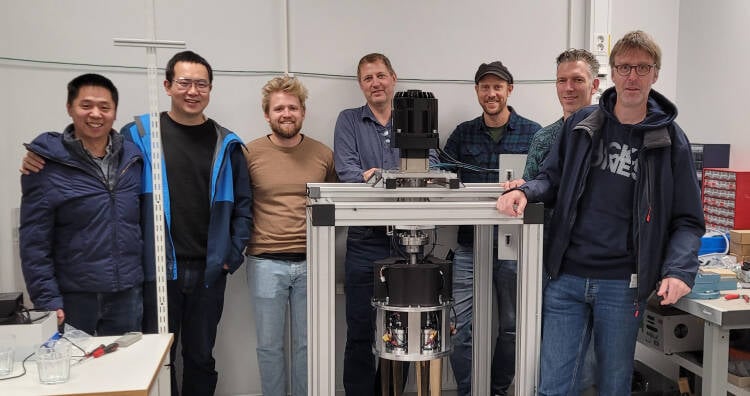
René Bosman
Senior Specialist Mechanical Measurement, MARIN
Jie Dang
Senior Project Manager, MARIN
Whale Tail Wheel
Inspired by these early studies, the Whale Tail Wheel (WTW) propulsion system was developed later at MARIN (Figure 2). Instead of vertical fins, this system consisted of horizontally placed fins spanning up to the ship’s width, rotating via orbit discs and following optimised trochoidal motions (Van Manen and Van Terwisga 1996). With its large propulsion area and low thrust loading, combined with low rotation rates to reduce viscous losses, the WTW achieved an impressive 84% open-water efficiency. Subsequent studies confirmed that it had better cavitation performance, noting that low thrust loading also minimised cavitation risks and enhanced practical applicability.
Figure 2. A Whale Tail Wheel (TWT) scale model in MARIN’s cavitation tunnel (1996).
Figure 1. Test equipment for vertical axis propellers in a cavitation tunnel at NSMB (1963).
June 2025, no. 144
First systematic tests in 1963
MARIN, then known as the Netherlands Ship Model Basin (NSMB), performed the first systematic tests on vertical fin propulsors in 1963 (Figure 1), featuring various fin blades and motions (Van Manen 1966). In addition to a standard cycloidal motion, governed by an eccentricity-radius ratio ‘e’ of all fin normals, significant improvements were found by applying a so-called Sparenberg’s optimum criterion, which maintained constant bound circulation on the fins to minimise energy losses by preventing transverse vortex shedding.
The µMMS is not only applicable for FOWT, but also for other small floaters and ships. The new measurement system makes it possible to accurately test small vessels, without the unwanted effect of the measurement cables.
For example, this year the Dutch Ministry of Infrastructure and Water Management contracted MARIN to investigate the dynamics that are involved in the capsizing of beam trawlers. The main goal of this project was to investigate the capsize risk in relation to fishing operations and the stability criteria.
Initially, we had planned to make a free sailing model for the tests that connects to the measurement system on the carriage. The combination of a small vessel and the high wave height in the tests resulted in a model weight of less than 100 kg. Given the small model size, low forces can have an impact on the rolling behaviour of the vessel. Therefore, to minimise the impact that the cables can have on the motions of the vessel, we minimised the number of sensors on board to the bare minimum. Additionally, we planned to use thinner cables than normal to reduce the weight even further.
The µMMS became available when we were designing the model. This offered the opportunity to make the model completely wireless and to measure more signals within the budget of the project. Without the measurement wires between the carriage and the model, the test setup was more versatile. No precautions were necessary to avoid interference from the measurement cables.
This required higher pitch angles in the slipstream coming from the first half of a cycle. These early tests explored not only low-pitch epi-cycloidal fin motions (e < 1, P/D < π, circumferential velocity > advance velocity) such as the VSPs, but also high-pitch trochoidal motions (e > 1, P/D > π, circumferential velocity < advance velocity). These model tests already demonstrated high open-water efficiencies up to 70% for trochoidal motions.
Vertical fin propulsors have been in operation since June 1931 when the first Voith Schneider Propulsor (VSP) was fitted to a ship (Jürgens 2002). Renowned for their superior manoeuvrability and roll-damping capabilities, VSPs were deployed widely over the years. And recently they have attracted attention again. Interest in fin propulsion has resurged, but this time with a focus on achieving exceptionally high efficiency through optimised fin motions.
Fin propulsion is experiencing a revival due to its high propulsive efficiency. In early 2025, MARIN successfully tested a new fully electric system – an ABB DynafinTM.
Fin propulsion revival
Create a MARIN account to stay updated
