News
Shallow water
EEXI
Wind propulsion
Turbulent breakthrough
CFD VIM
Floating Wind
Shortsea shipping
Cover
Create a MARIN account to stay updated
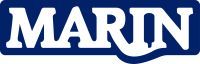
Comparison between CFD and EFD propeller open-water performance with and without turbulence stimulation.
Abridged video of open-water propeller paint test (Courtesy ABB).
December 2023, no. 138
More info
This need has led to the Tripping Joint Industry Project that aims to provide a dataset to benchmark CFD simulations for propellers and generate new generic extrapolation procedures to predict full-scale powering performance. This approach is expected to reflect the effects of Reynolds scale more accurately on lift and drag, bridging the gap between model-scale tests and real-world propeller performance. New participants to the Tripping JIP are welcome to join and work together on a reliable basis for future powering predictions, either using model tests or CFD computations (www.marin.nl/jips/tripping).
As we advance towards more efficient and complex propulsion systems, our improved understanding of model propeller boundary layer dynamics marks a significant achievement. The advancements in propeller paint test procedures and the innovative use of turbulators have laid a solid foundation for more accurate model testing. Enhanced transition modelling in our CFD simulations has furthered our ability to predict real-world propeller performance more precisely. The upcoming Tripping JIP represents a crucial step in refining our extrapolation methods, contributing to the development of better ships and blue oceans.
For technical details, please refer to the following future publications.
Schuiling B., Kerkvliet M., Rijpkema D. (2024), An Experimental Study on Visualisation and Passive Control of Model Propeller Boundary Layers, Eighth International Symposium on Marine Propulsors (SMP’24, not yet published)
Kerkvliet M., Baltazar J., Schuiling B. and Eça L. (2024), A Numerical Study on Model Propeller Performance Prediction Including Transitional and Passively Controlled Boundary Layer Considerations, Eighth International Symposium on Marine Propulsors (SMP’24, not yet published)
The enhanced visualisation of the boundary layer has also been crucial in improving our viscous flow Computational Fluid Dynamics (CFD) simulations. Through our long-term collaboration with IST University of Lisbon, MARIN has successfully integrated transition-sensitive turbulence models into our CFD solver, ReFRESCO. These advanced models are adept at capturing the onset and full extent of transition. They also accurately reflect the associated changes in skin friction, pressure distribution, and wake formation. Our research has emphasised the necessity of incorporating transition modelling in CFD to accurately predict the propeller performance at model-scale in case no turbulation stimulation is used. However, when turbulators are employed during experiments, propellers can effectively be modelled using the default fully turbulent flow models.
Both the improved transition modelling for the CFD and the new turbulators have reduced the difference between CFD and experiments and increased the confidence in the numerical-based propeller performance predictions. Therefore, the research on model propeller boundary layers has paved the way towards CFD-based extrapolation methods for propeller performance.
Participants welcome for Tripping JIP
However, despite advancements in CFD, the maritime industry still seeks practical methods to accurately scale model test results to full-scale for predicting ship propeller performance.
To address these inconsistencies and enhance the reliability of model testing procedures, MARIN is exploring the advantages of applying turbulence stimulators - dubbed turbulators - to model propellers. By employing turbulators, a turbulent boundary layer can be consistently achieved. While this technique is already standard practice for model ships and their appendages, its application to propellers has not yet been adopted in the ITTC guidelines and procedures.
Turbulation and simulation advances
In this context, MARIN has pioneered two innovative approaches. The first is a new type of cost-effective turbulator. This method efficiently induces a turbulent boundary layer and enhances the repeatability and accuracy of testing procedures. The second innovation is a refined experimental method for conducting propeller paint tests, significantly improving our ability to visualise the propeller boundary layer flow. The new paint formulation was developed from more than 300 systematic experiments. This ensures precise near wall flow visualisation tailored to specific Reynolds numbers. The paint facilitates detailed analysis of boundary layer transition, separation and the effectiveness of the turbulators
Improving propeller performance tests
The implications of this issue are profound: a turbulent boundary layer fundamentally alters propeller performance. This effect is most evident in terms of lift, a critical aspect. Furthermore, the laminar boundary layers typically observed at model scale tend to separate near the trailing edge, also drastically influencing the model propeller performance. This is another critical factor not adequately addressed in model-to-full-scale extrapolations. These discrepancies suggest that a propeller, while performing optimally in model tests, may not deliver comparable efficiency in real-world, full-scale scenarios. This calls into question the efficacy of current model testing methods, especially when comparing different propeller designs and the measured differences are marginal.
In this research, we reinvented an Experimental Fluid Dynamics (EFD) method to visualise propeller boundary layer flow using paint, refined Computational Fluid Dynamics (CFD) simulations, and developed an innovative approach to stimulate turbulence in propeller models. These advancements are not just academic; they promise practical improvements in maritime model testing. This article will explore the intricacies of this groundbreaking method and its far-reaching implications for the maritime industry.
In our quest to improve the accuracy and reduce the uncertainty of model tests, we have confronted a key challenge: the nature of the propeller's boundary layer during model tests. Since the 1940s, MARIN has recognised that model propeller boundary layers are often laminar or partially laminar during model tests. This is a problem because it does not represent the full-scale turbulent flow, which is what the model tests are intended to simulate in order to predict the performance of the propeller.
Report
new standards
for model propeller testing
What if a small modification could dramatically enhance the accuracy, interpretability and reliability of model tests used to predict ship performance? This is not mere fiction, but the result of three years of intensive research into model propeller boundary layers.
Boundary layer visualisation at design condition using EFD with turbulators at the leading edge operating at 400 rpm.
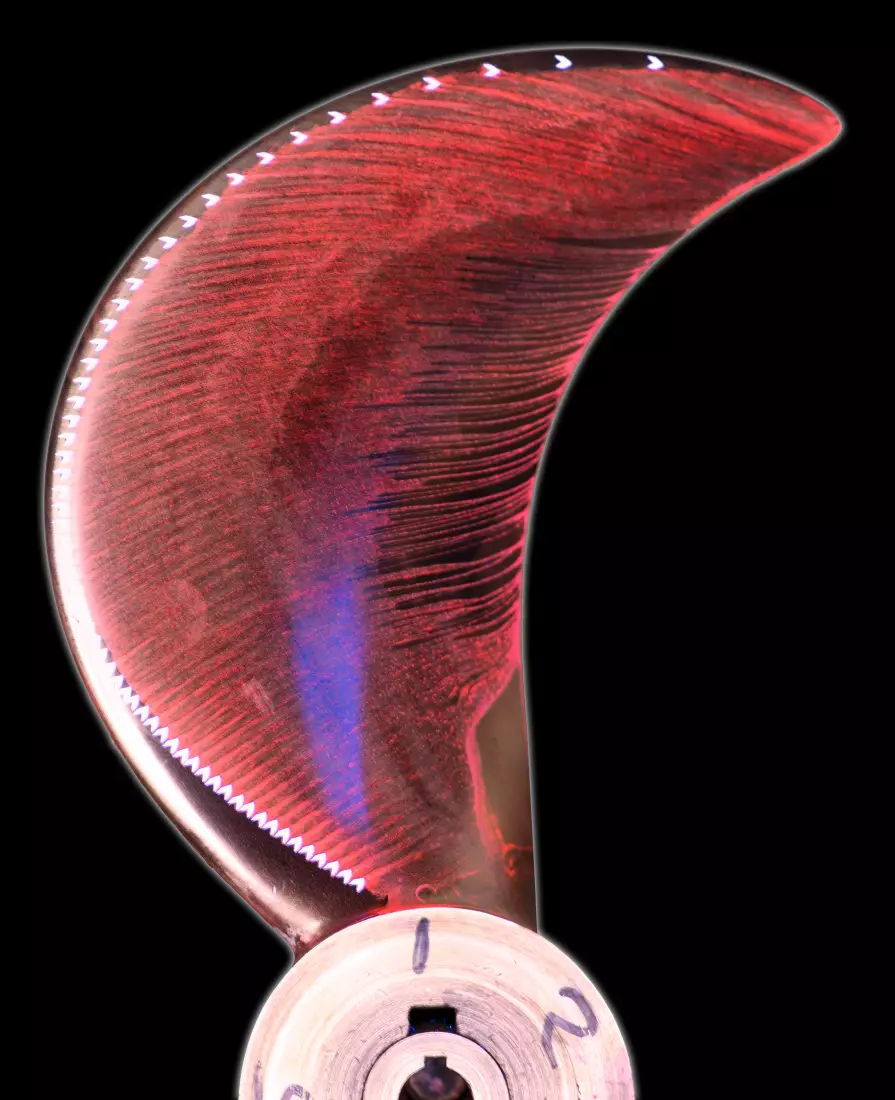
Boundary layer visualisation at design condition using CFD, assuming fully turbulent flow operating at 400 rpm.
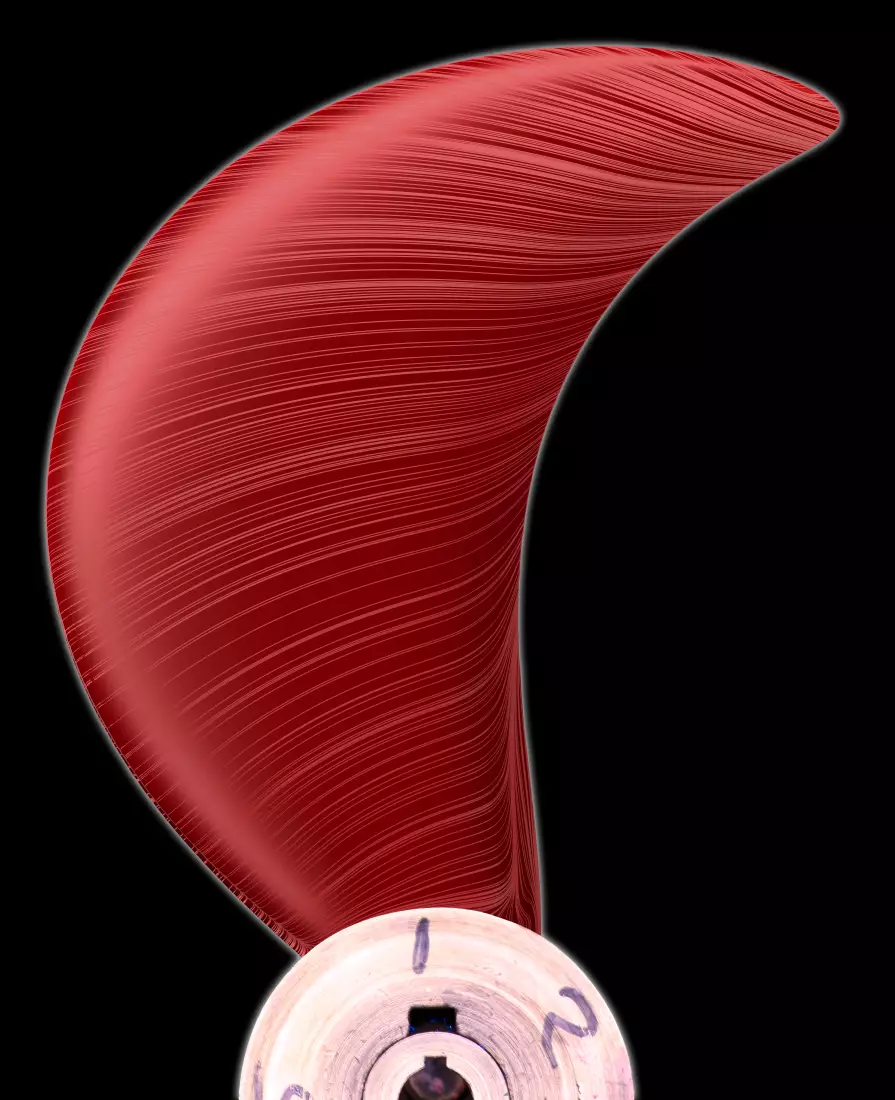
Boundary layer visualisation at design condition using EFD without turbulence stimulation operating at 400 rpm.
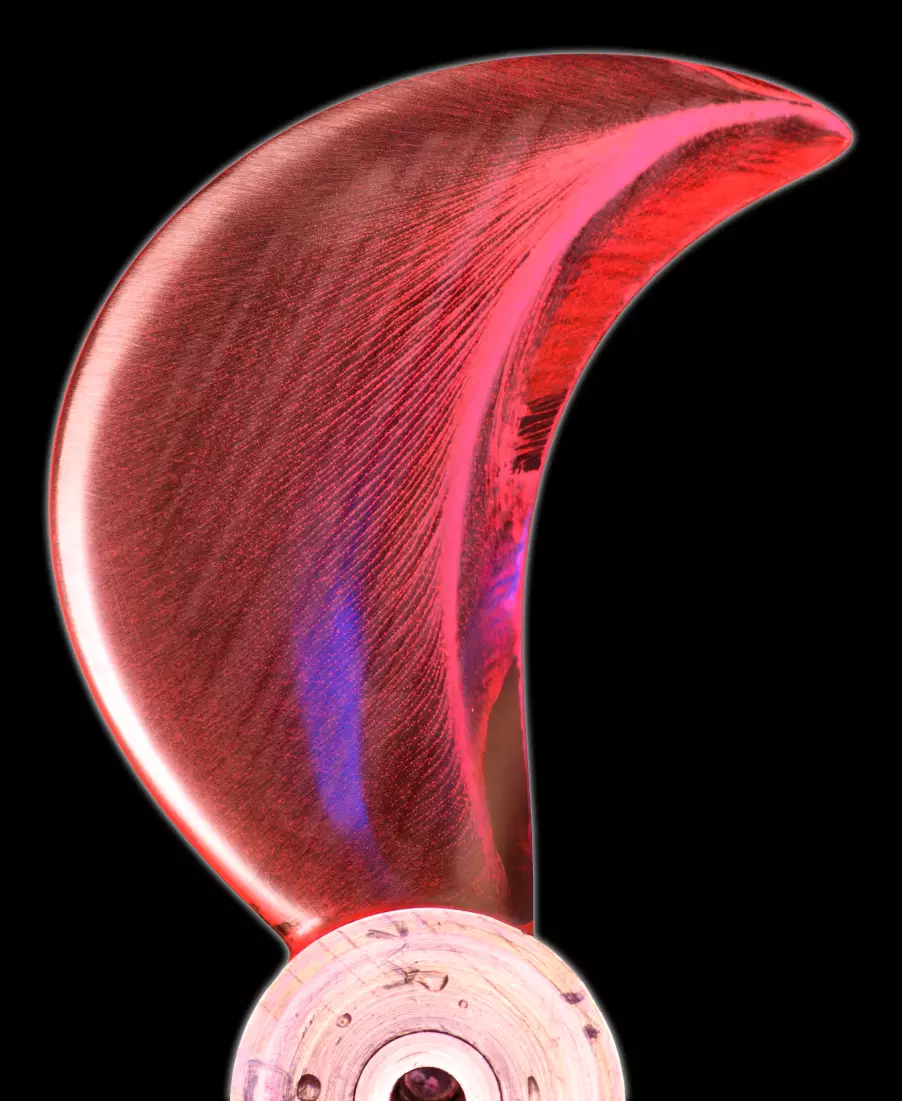
Boundary layer visualisation at design condition using CFD, including transition modelling operating at 400 rpm.
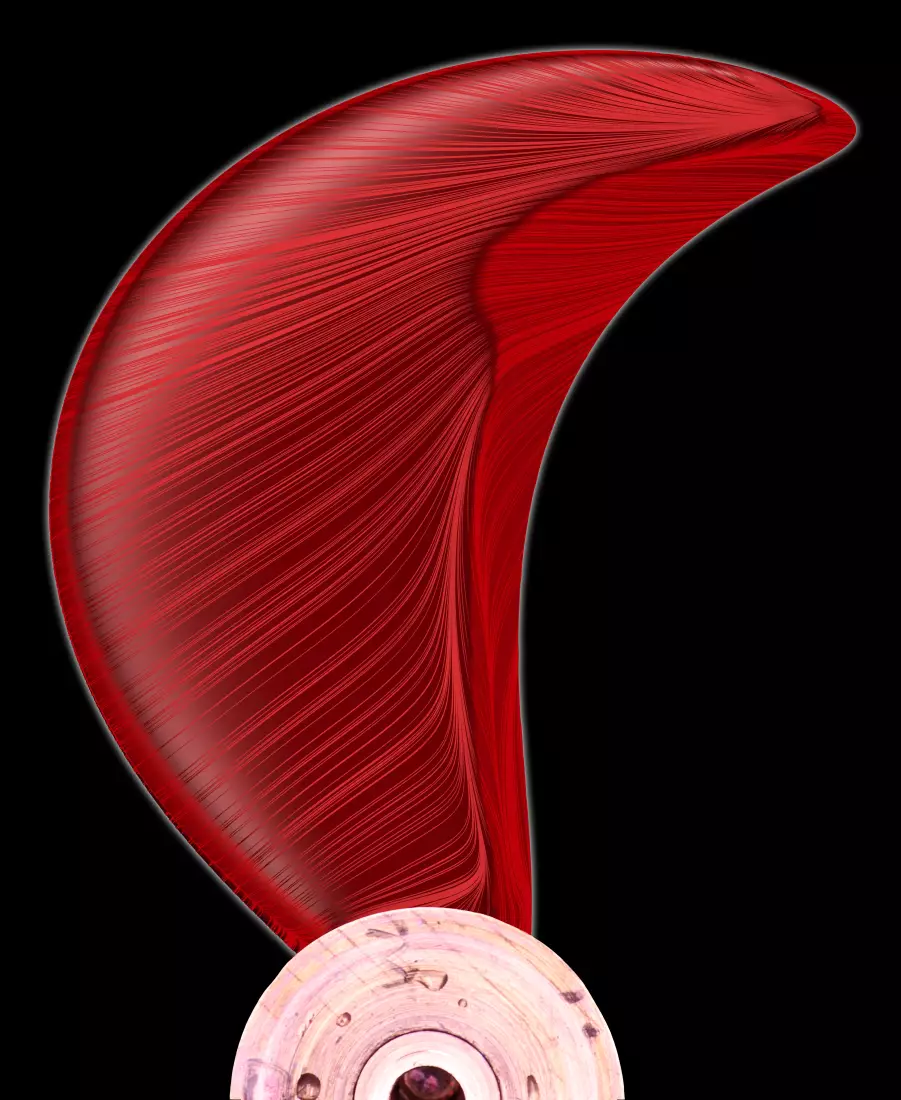
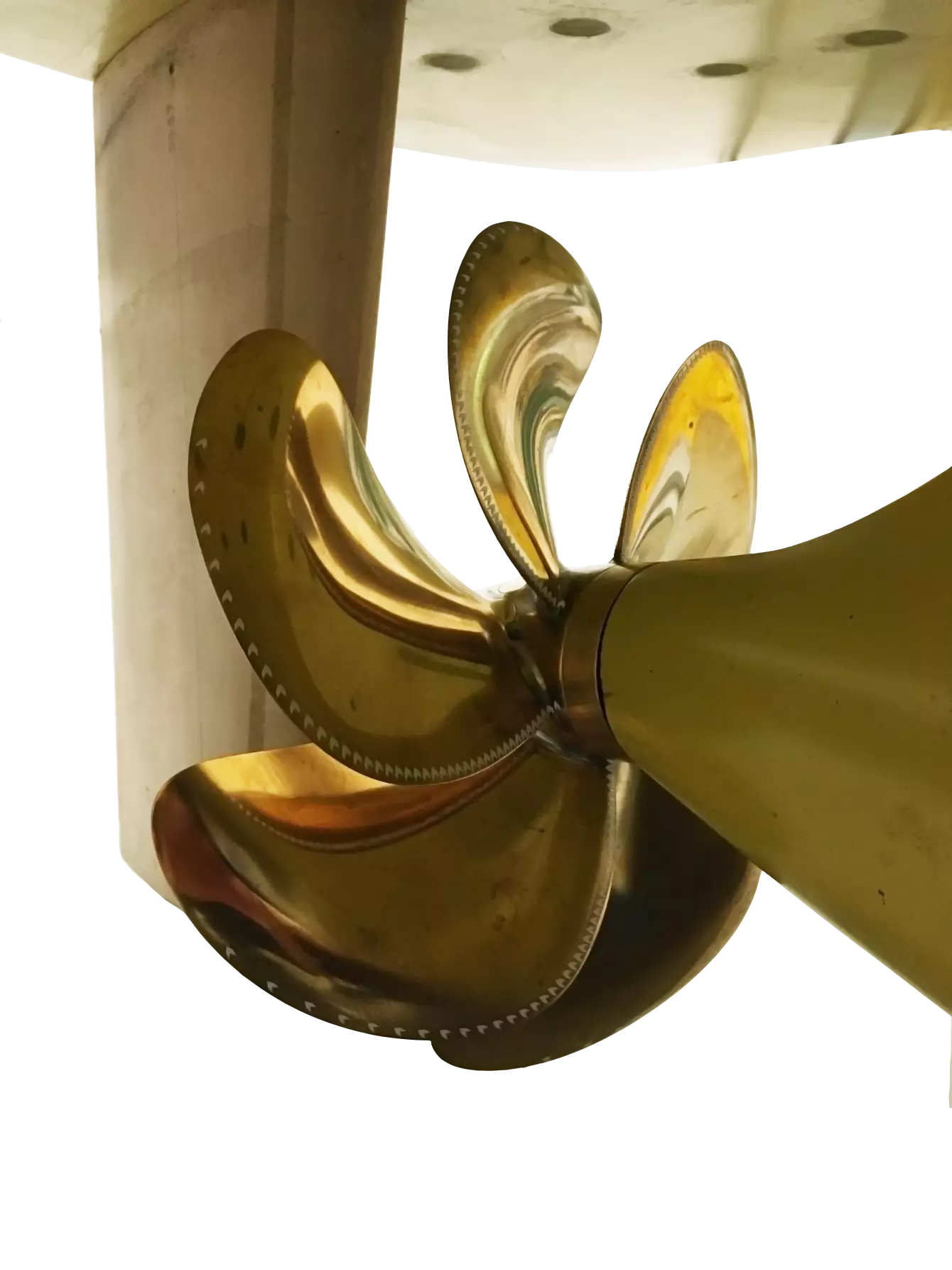
full-scale powering performance.”
Tripping Joint Industry Project
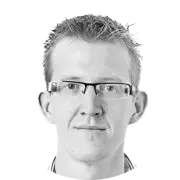
Bart Schuiling
Senior Researcher
full-scale powering performance.”
This need has led to the Tripping Joint Industry Project that aims to provide a dataset to benchmark CFD simulations for propellers and generate new generic extrapolation procedures to predict full-scale powering performance. This approach is expected to reflect the effects of Reynolds scale more accurately on lift and drag, bridging the gap between model-scale tests and real-world propeller performance. New participants to the Tripping JIP are welcome to join and work together on a reliable basis for future powering predictions, either using model tests or CFD computations (www.marin.nl/jips/tripping).
As we advance towards more efficient and complex propulsion systems, our improved understanding of model propeller boundary layer dynamics marks a significant achievement. The advancements in propeller paint test procedures and the innovative use of turbulators have laid a solid foundation for more accurate model testing. Enhanced transition modelling in our CFD simulations has furthered our ability to predict real-world propeller performance more precisely. The upcoming Tripping JIP represents a crucial step in refining our extrapolation methods, contributing to the development of better ships and blue oceans.
For technical details, please refer to the following future publications.
Schuiling B., Kerkvliet M., Rijpkema D. (2024), An Experimental Study on Visualisation and Passive Control of Model Propeller Boundary Layers, Eighth International Symposium on Marine Propulsors (SMP’24, not yet published)
Kerkvliet M., Baltazar J., Schuiling B. and Eça L. (2024), A Numerical Study on Model Propeller Performance Prediction Including Transitional and Passively Controlled Boundary Layer Considerations, Eighth International Symposium on Marine Propulsors (SMP’24, not yet published)
Comparison between CFD and EFD propeller open-water performance with and without turbulence stimulation.
The enhanced visualisation of the boundary layer has also been crucial in improving our viscous flow Computational Fluid Dynamics (CFD) simulations. Through our long-term collaboration with IST University of Lisbon, MARIN has successfully integrated transition-sensitive turbulence models into our CFD solver, ReFRESCO. These advanced models are adept at capturing the onset and full extent of transition. They also accurately reflect the associated changes in skin friction, pressure distribution, and wake formation. Our research has emphasised the necessity of incorporating transition modelling in CFD to accurately predict the propeller performance at model-scale in case no turbulation stimulation is used. However, when turbulators are employed during experiments, propellers can effectively be modelled using the default fully turbulent flow models.
Both the improved transition modelling for the CFD and the new turbulators have reduced the difference between CFD and experiments and increased the confidence in the numerical-based propeller performance predictions. Therefore, the research on model propeller boundary layers has paved the way towards CFD-based extrapolation methods for propeller performance.
Participants welcome for Tripping JIP
However, despite advancements in CFD, the maritime industry still seeks practical methods to accurately scale model test results to full-scale for predicting ship propeller performance.
Abridged video of open-water propeller paint test (Courtesy ABB).
Boundary layer visualisation at design condition using EFD with turbulators at the leading edge operating at 400 rpm.
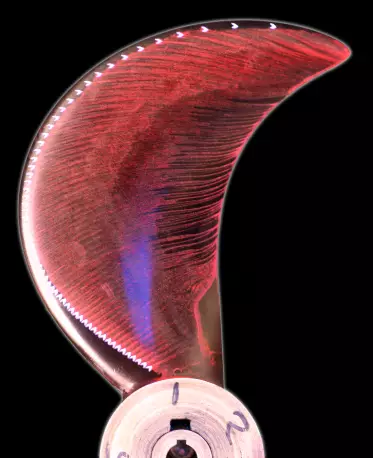
Boundary layer visualisation at design condition using CFD, assuming fully turbulent flow operating at 400 rpm.
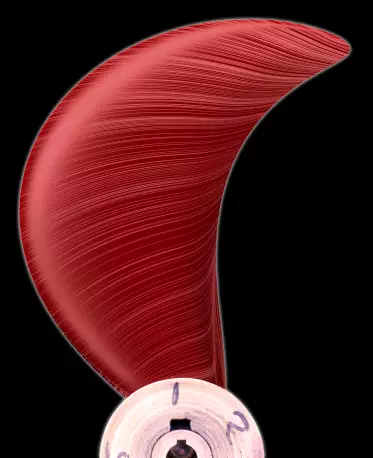
To address these inconsistencies and enhance the reliability of model testing procedures, MARIN is exploring the advantages of applying turbulence stimulators - dubbed turbulators - to model propellers. By employing turbulators, a turbulent boundary layer can be consistently achieved. While this technique is already standard practice for model ships and their appendages, its application to propellers has not yet been adopted in the ITTC guidelines and procedures.
Turbulation and simulation advances
In this context, MARIN has pioneered two innovative approaches. The first is a new type of cost-effective turbulator. This method efficiently induces a turbulent boundary layer and enhances the repeatability and accuracy of testing procedures. The second innovation is a refined experimental method for conducting propeller paint tests, significantly improving our ability to visualise the propeller boundary layer flow. The new paint formulation was developed from more than 300 systematic experiments. This ensures precise near wall flow visualisation tailored to specific Reynolds numbers. The paint facilitates detailed analysis of boundary layer transition, separation and the effectiveness of the turbulators
Boundary layer visualisation at design condition using EFD without turbulence stimulation operating at 400 rpm.
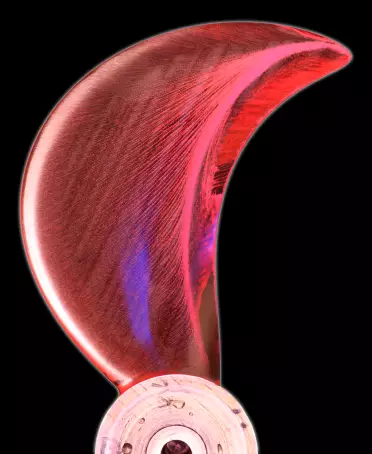
Boundary layer visualisation at design condition using CFD, including transition modelling operating at 400 rpm.
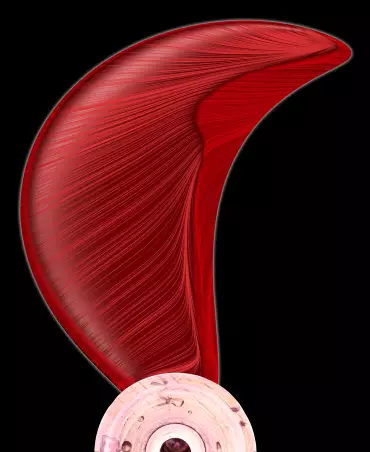
Improving propeller performance tests
The implications of this issue are profound: a turbulent boundary layer fundamentally alters propeller performance. This effect is most evident in terms of lift, a critical aspect. Furthermore, the laminar boundary layers typically observed at model scale tend to separate near the trailing edge, also drastically influencing the model propeller performance. This is another critical factor not adequately addressed in model-to-full-scale extrapolations. These discrepancies suggest that a propeller, while performing optimally in model tests, may not deliver comparable efficiency in real-world, full-scale scenarios. This calls into question the efficacy of current model testing methods, especially when comparing different propeller designs and the measured differences are marginal.
new standards
for model propeller testing
Report
December 2023,
no. 138
Create a MARIN account to stay updated
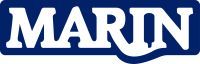
Tripping Joint Industry Project
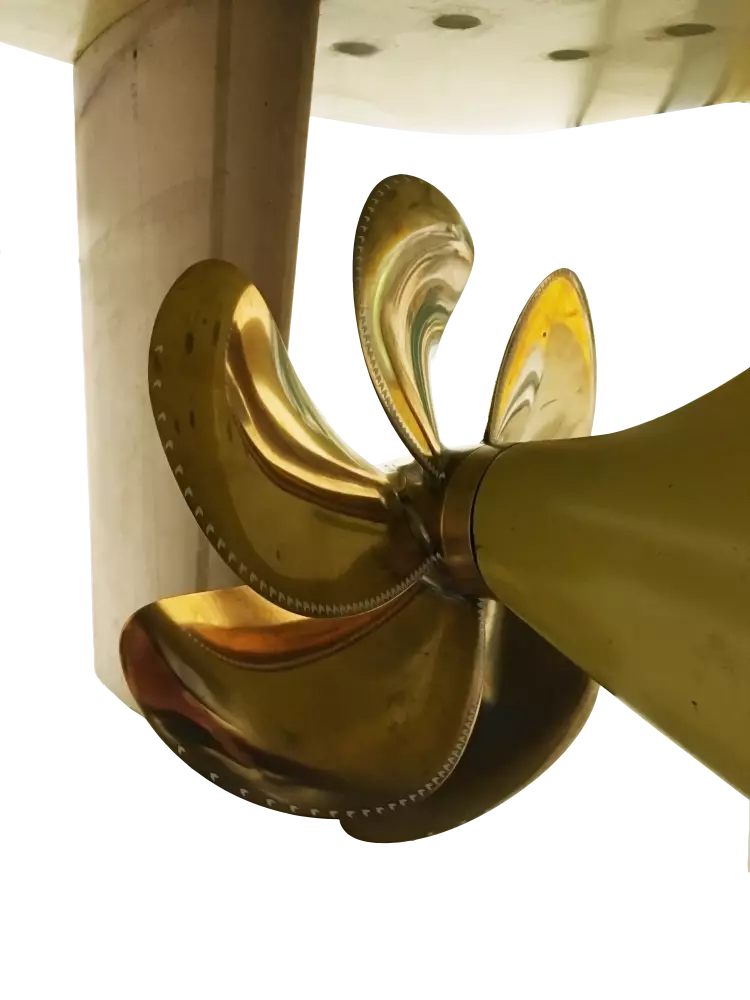
More info
In this research, we reinvented an Experimental Fluid Dynamics (EFD) method to visualise propeller boundary layer flow using paint, refined Computational Fluid Dynamics (CFD) simulations, and developed an innovative approach to stimulate turbulence in propeller models. These advancements are not just academic; they promise practical improvements in maritime model testing. This article will explore the intricacies of this groundbreaking method and its far-reaching implications for the maritime industry.
In our quest to improve the accuracy and reduce the uncertainty of model tests, we have confronted a key challenge: the nature of the propeller's boundary layer during model tests. Since the 1940s, MARIN has recognised that model propeller boundary layers are often laminar or partially laminar during model tests. This is a problem because it does not represent the full-scale turbulent flow, which is what the model tests are intended to simulate in order to predict the performance of the propeller.
What if a small modification could dramatically enhance the accuracy, interpretability and reliability of model tests used to predict ship performance? This is not mere fiction, but the result of three years of intensive research into model propeller boundary layers.