Visualisation of CFD computation on bulk carrier fitted with rotor sails.
Modelling of aerodynamic interaction effects for wind propulsion applied in commercial shipping development of a non-linear lifting line method
Holistic approach design and optimisation for wind-assisted ship propulsion
More info
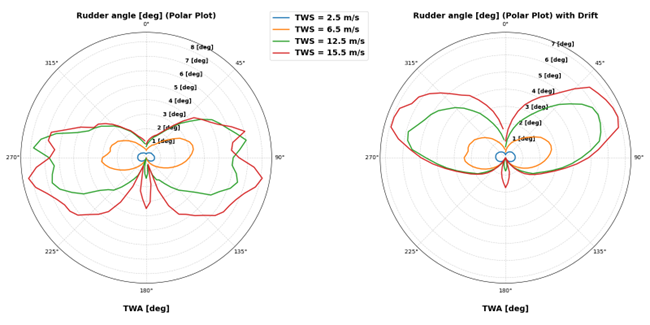
Figure 4. Polar plots of rudder and drift angles.
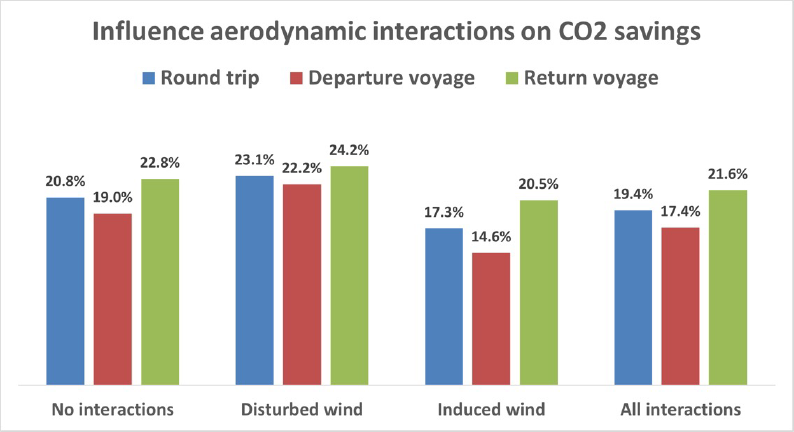
Figure 3. Influence of the aerodynamic interaction effects on the CO2 savings.
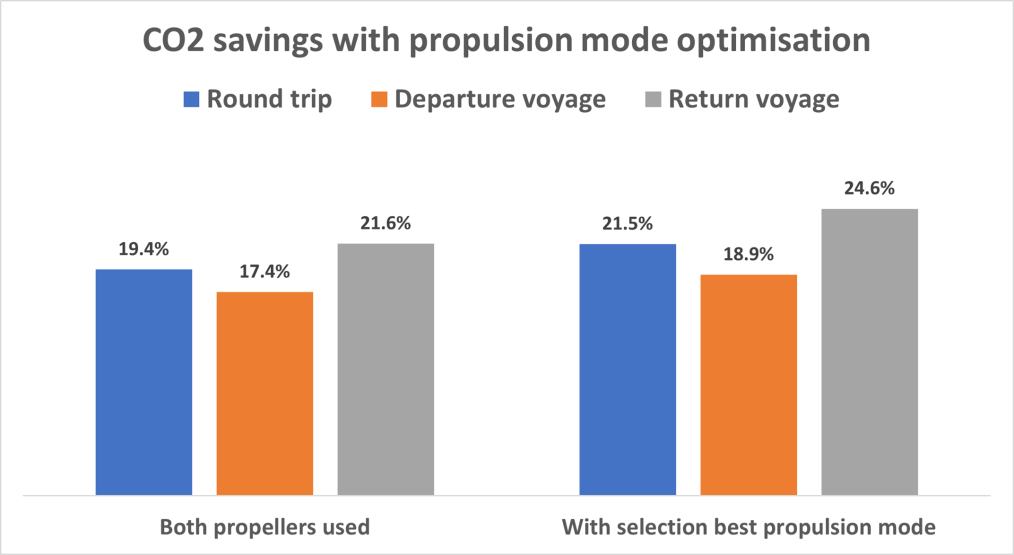
Figure 2. CO2 savings with and without propulsion mode optimisation, i.e. letting one propeller run in feathering mode when beneficial.
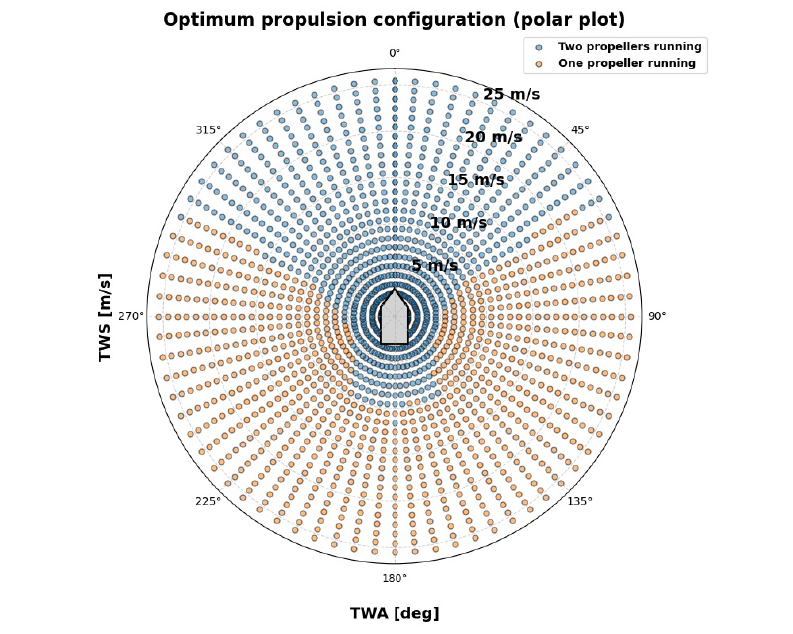
Figure 1. Optimum propulsion mode per wind condition.
March 2025, no. 143
Create a MARIN account to stay updated
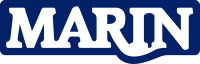
Report
These are both exciting and challenging times for the shipping industry, which is gradually embracing wind propulsion as a powerful tool to decarbonise the global fleet. As an independent research institute, MARIN provides advice and clarity with respect to wind propulsion technology by covering all aspects of ship design, from the concept phase to the monitoring of operations on board. For these services, MARIN has developed a set of numerical and experimental tools to deliver reliable wind propulsion performance predictions.
MARIN is proactively taking part in several initiatives such as BlueRoute which is a software tool for predicting wind propulsion performance. This is freely accessible for basic functionality, with more advanced features available in the paid section.
Supporting
clients with reliable
wind propulsion
performance predictions
The wind propulsion market continues to accelerate, with the fleet of commercial ships equipped with wind propulsion technology doubling in the last year. The prospects for future retrofit and newbuild installations are also looking promising with several recent announcements.
CFD simulations
Using a combination of hydrodynamic and aerodynamic CFD simulations, the Wageningen
C-series and the PPP/VPP program SAILFISH, MARIN addressed the questions from STENA within a lead time of less than three to four weeks. An interesting challenge was the possibility to optimise the Power Propulsion and Energy systems’ function of the operating conditions. The results from this optimisation process are illustrated in figure 1 and 2 in which it can be seen that for reaching and running conditions with more than 7.5m/sec of wind, the vessel operates more efficiently with one propeller in feathering mode.
One constraint imposed by STENA was to keep the heel within 2 degrees and include the action of the anti-heeling tanks. It was found that up to Beaufort 7, the vessel can keep this constraint without having to depower the sails. STENA indicated that the study should include the aerodynamic interaction effects between the superstructures and the wind propulsion, which was conducted using the method described in modelling of aerodynamic interaction effects1.
One added value of this method is the possibility to distinguish the influence of the different aerodynamic interaction effects on the overall savings, see figure 3. Finally, it was important for STENA to understand how good the yaw balance of the vessel is. To do so, MARIN analysed the polars of the leeway and rudder angle, see figure 4 which indicated that limited rudder angles are required.
Other examples include the numerous numerical performance prediction studies MARIN conducts for ships equipped with wind propulsion. These studies are typically carried out during the concept and design phases or as retrofit activities. Common questions addressed involve fuel savings, heel/yaw balance, and the efficiency of the global ship system. These studies often serve as a valuable foundation for calculating the EEDI, EEXI and CII.
STENA case study
An interesting example of such a study is one performed on behalf of STENA, where MARIN was asked to estimate the fuel performance of a wind propulsion vessel fitted with controllable pitch propellers.
STENA was interested in high fidelity fuel saving estimations accounting for the added resistance due to the weather conditions, as well as the hydrodynamic-aerodynamic interactions which affect the overall performance of the vessel. Using the recommended terminology from the ITTC 75-02-03-019, the request from STENA translates into a prediction of fidelity Level III.
BlueWeek in April
You are very welcome to contact us if you are interested in learning more about these initiatives. It is also worth noting that the upcoming BlueWeek, organised in Wageningen, will take place between April 7 - 11. BlueWeek is an open platform to discuss ongoing innovations and projects, as well as new initiatives.
Wind propulsion performance assessment
While the results and methods from ongoing development projects will still require a few years to be finalised, MARIN already uses the accumulated experiences to help the industry with today’s challenges. One excellent illustration of this is the newly adopted hybrid tank testing, as described in the previous article covering the project with Deltamarin and NorsePower for Louis Dreyfus Armateurs.
Predicting fuel savings
The WISP3 JIP kicked-off in 2024 and will run until mid-2026. WISP3 focuses on the standardisation of performance predictions for wind propulsion and updating the regulations (EEDI, EEXI, CII and IMO Resolution MSC 137(76)). The goal is to define industry standards to predict fuel savings.
MARIN is also delighted to contribute to the benchmarking efforts of the JIP SWOPP, initiated by RISE. Additionally, MARIN is collaborating with several partners within the EU project OPTIWISE to develop new holistic design and control methods to create new ship concepts utilising wind propulsion to its maximum potential.
Interested? Contact us to discuss your options
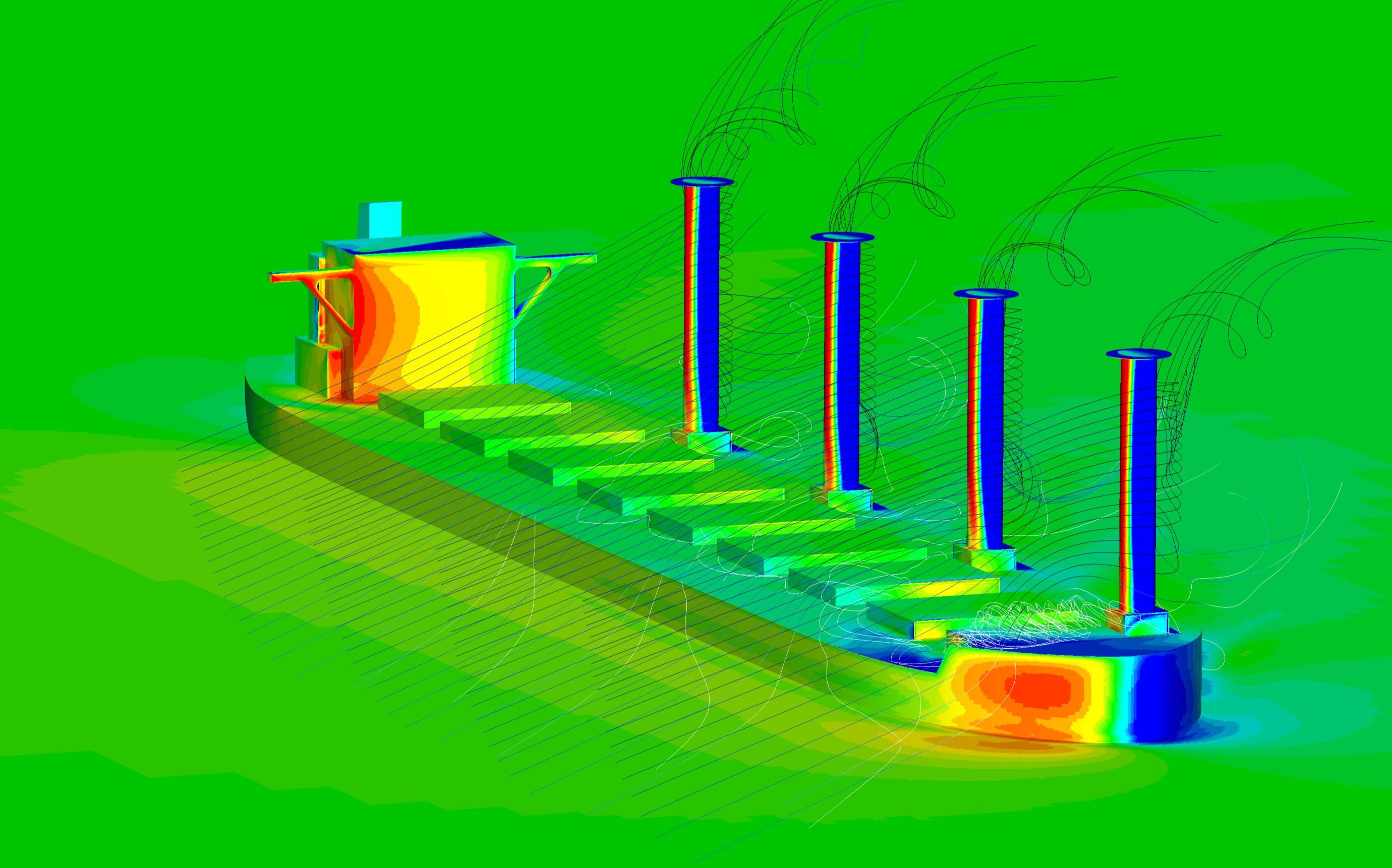
More info
Holistic approach design and optimisation for wind-assisted ship propulsion
One constraint imposed by STENA was to keep the heel within 2 degrees and include the action of the anti-heeling tanks. It was found that up to Beaufort 7, the vessel can keep this constraint without having to depower the sails. STENA indicated that the study should include the aerodynamic interaction effects between the superstructures and the wind propulsion, which was conducted using the method described in modelling of aerodynamic interaction effects1.
One added value of this method is the possibility to distinguish the influence of the different aerodynamic interaction effects on the overall savings, see figure 3. Finally, it was important for STENA to understand how good the yaw balance of the vessel is. To do so, MARIN analysed the polars of the leeway and rudder angle, see figure 4 which indicated that limited rudder angles are required.
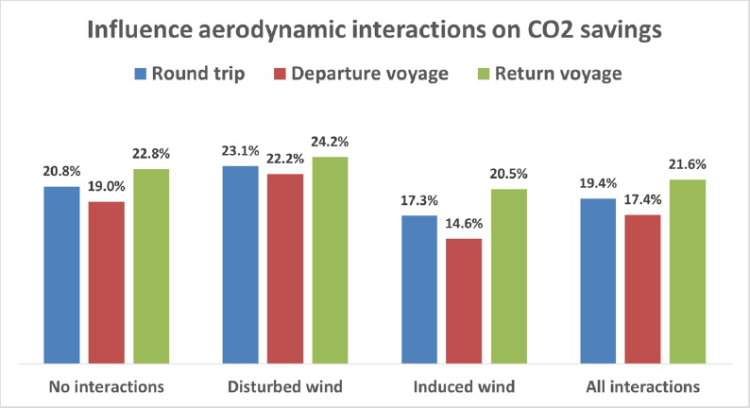
Figure 3. Influence of the aerodynamic interaction effects on the CO2 savings.
Other examples include the numerous numerical performance prediction studies MARIN conducts for ships equipped with wind propulsion. These studies are typically carried out during the concept and design phases or as retrofit activities. Common questions addressed involve fuel savings, heel/yaw balance, and the efficiency of the global ship system. These studies often serve as a valuable foundation for calculating the EEDI, EEXI and CII.
STENA case study
An interesting example of such a study is one performed on behalf of STENA, where MARIN was asked to estimate the fuel performance of a wind propulsion vessel fitted with controllable pitch propellers.
STENA was interested in high fidelity fuel saving estimations accounting for the added resistance due to the weather conditions, as well as the hydrodynamic-aerodynamic interactions which affect the overall performance of the vessel. Using the recommended terminology from the ITTC 75-02-03-019, the request from STENA translates into a prediction of fidelity Level III.
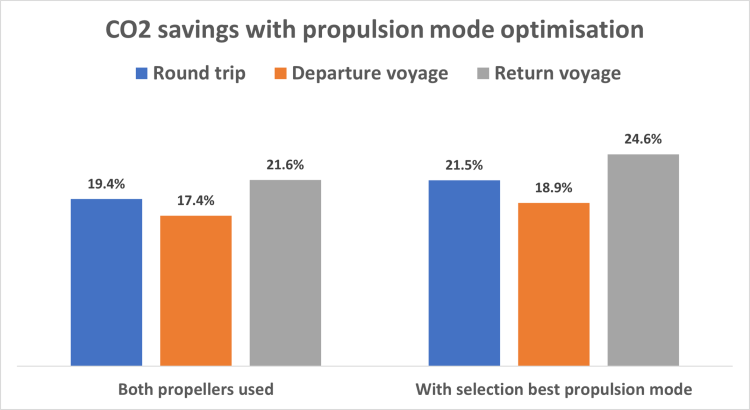
Figure 2. CO2 savings with and without propulsion mode optimisation, i.e. letting one propeller run in feathering mode when beneficial.
BlueWeek in April
You are very welcome to contact us if you are interested in learning more about these initiatives. It is also worth noting that the upcoming BlueWeek, organised in Wageningen, will take place between April 7 - 11. BlueWeek is an open platform to discuss ongoing innovations and projects, as well as new initiatives.
Wind propulsion performance assessment
While the results and methods from ongoing development projects will still require a few years to be finalised, MARIN already uses the accumulated experiences to help the industry with today’s challenges. One excellent illustration of this is the newly adopted hybrid tank testing, as described in the previous article covering the project with Deltamarin and NorsePower for Louis Dreyfus Armateurs.
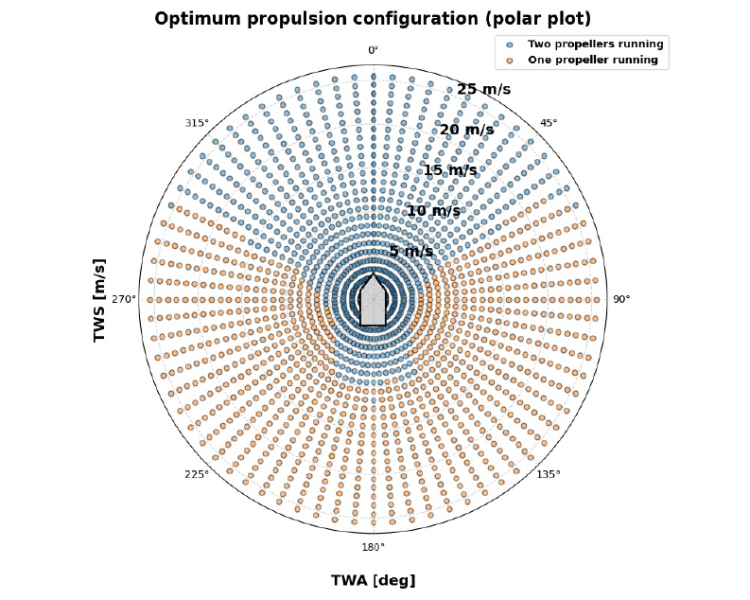
Figure 1. Optimum propulsion mode per wind condition.
March 2025, no. 143
Maxime Garenaux
Project Manager
Predicting fuel savings
The WISP3 JIP kicked-off in 2024 and will run until mid-2026. WISP3 focuses on the standardisation of performance predictions for wind propulsion and updating the regulations (EEDI, EEXI, CII and IMO Resolution MSC 137(76)). The goal is to define industry standards to predict fuel savings.
MARIN is also delighted to contribute to the benchmarking efforts of the JIP SWOPP, initiated by RISE. Additionally, MARIN is collaborating with several partners within the EU project OPTIWISE to develop new holistic design and control methods to create new ship concepts utilising wind propulsion to its maximum potential.
These are both exciting and challenging times for the shipping industry, which is gradually embracing wind propulsion as a powerful tool to decarbonise the global fleet. As an independent research institute, MARIN provides advice and clarity with respect to wind propulsion technology by covering all aspects of ship design, from the concept phase to the monitoring of operations on board. For these services, MARIN has developed a set of numerical and experimental tools to deliver reliable wind propulsion performance predictions.
MARIN is proactively taking part in several initiatives such as BlueRoute which is a software tool for predicting wind propulsion performance. This is freely accessible for basic functionality, with more advanced features available in the paid section.
The wind propulsion market continues to accelerate, with the fleet of commercial ships equipped with wind propulsion technology doubling in the last year. The prospects for future retrofit and newbuild installations are also looking promising with several recent announcements.
Visualisation of CFD computation on bulk carrier fitted with rotor sails.
Supporting
clients with reliable
wind propulsion
performance predictions
Interested? Contact us to discuss your options
Report
Create a MARIN account to stay updated
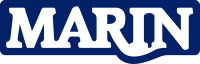
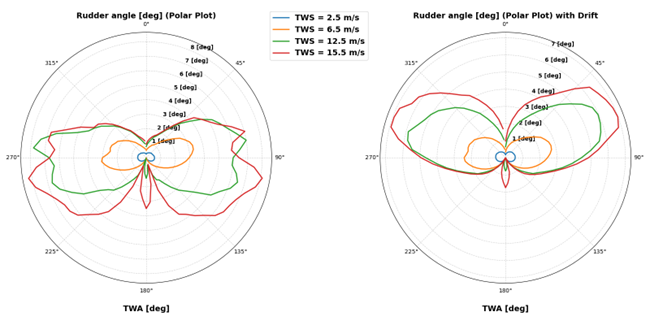
Figure 4. Polar plots of rudder and drift angles.
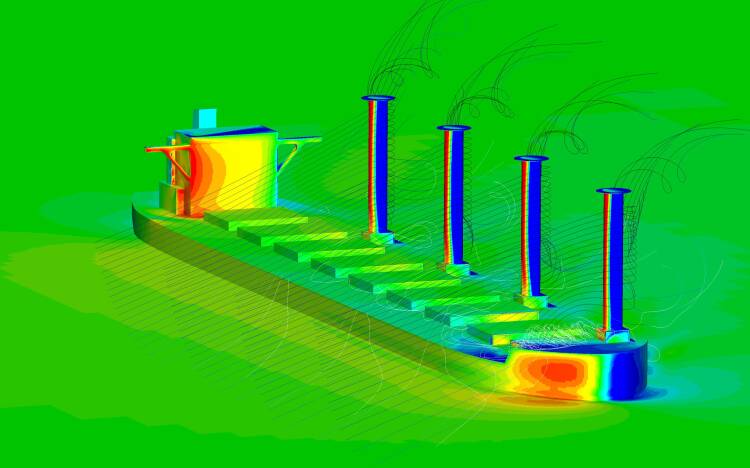