Interested? Contact us to discuss your options
Concept verification model tests for Friede & Goldman’s BargeRack system
December 2024, no. 142
https://www.fng.com/bargerack/
More info
Create a MARIN account to stay updated
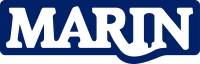
Figure 2: BargeRack model including vertical fenders (red) and horizontal fender system.
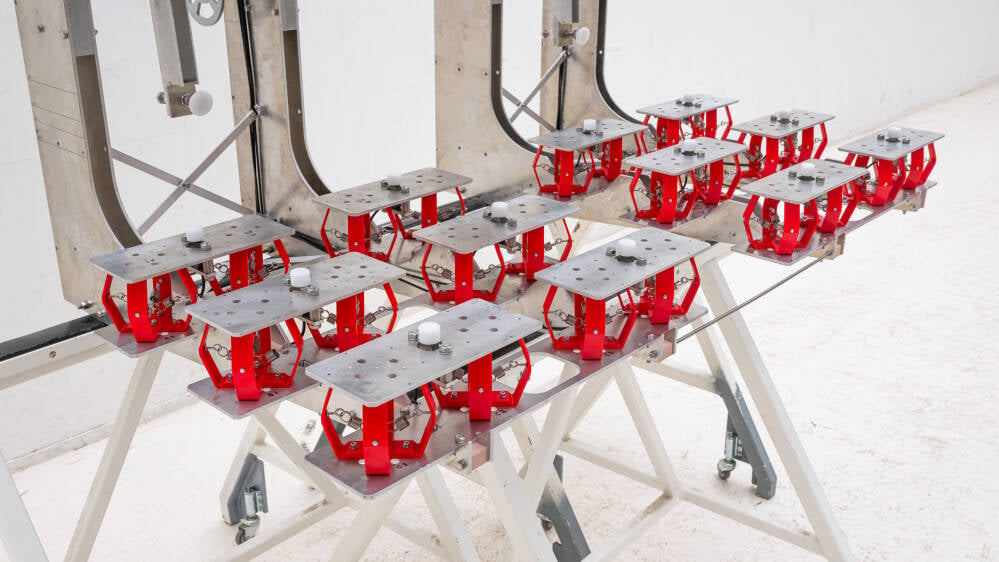
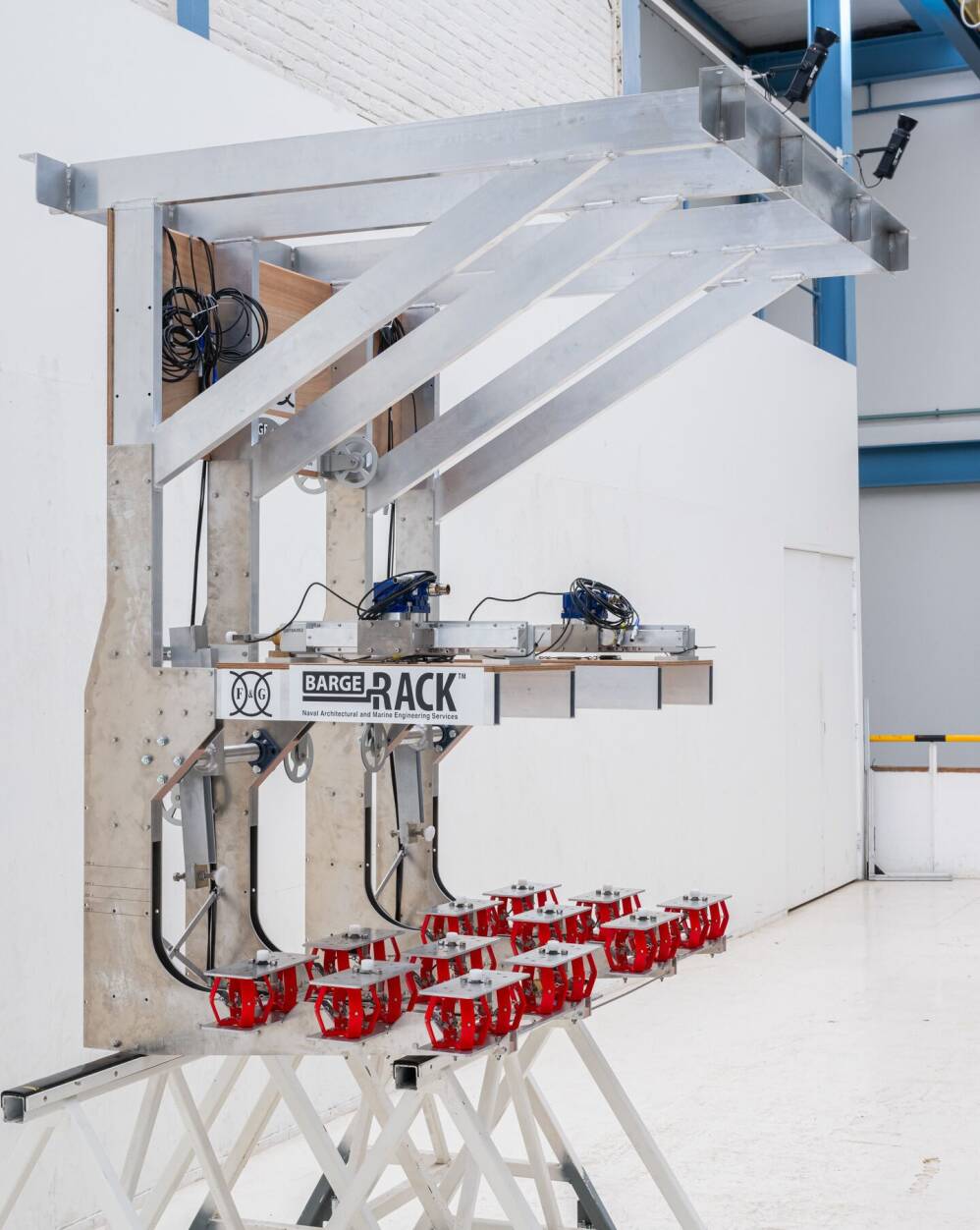
Report
The offshore wind industry is growing rapidly with an ever-increasing need for efficient, reliable, safe, and scalable installation solutions to help keep up with offshore wind developments. Compounded by port limitations, logistics bottlenecks, and cabotage laws there is more and more interest in wind turbine component feeder solutions to help meet this demand.
Figure 3: Barge and BargeRack models in the basin.
Figure 1: WTIV with the BargeRack Lifting Module.
Successful model testing
Impact loads measured during the model tests are in line with the results of the numerical simulations performed by Friede & Goldman. The concept verification model tests demonstrate the feasibility of the BargeRack solution and support Friede & Goldman in its development.
The successful completion of the model testing marks a major milestone for the BargeRack project. "We are excited to be one step closer to bringing this innovative solution to the market,” says Todd Allen, Director - Renewables at Friede & Goldman. “The success of the model testing reaffirms the significant benefit this technology can offer the offshore energy industry. The F&G team has worked closely with industry suppliers and fabricators to refine and ready the technology for deployment.”
Friede & Goldman have performed extensive hydrodynamic time domain simulations to determine the feeder vessel motions, dynamic impacts and the accelerations of the wind turbine components during the mating and lift. Structural simulations have been performed to guarantee the structural integrity of the BargeRack, feeder barge, and the WTIV. Earlier this year Approval in Principle (AiP) was received for the design.
More detailed insights in the BargeRack design and AiP assessment are given in Vidic-Perunovic et al. (2024).
Vertical and horizontal fenders
During the verification model tests the vertical and horizontal fender characteristics were represented in detail, as these are crucial for the motions of the feeder vessel and impact loads, while the DP system was not modelled and simplified by a string. The vertical fenders were 3D printed and represent the non-linear force-deflection characteristics of the full-scale fenders. The horizontal fenders characteristics were represented by active actuators.
The WTIV was not represented during the tests. Instead, the BargeRack was attached to the carriage by means of a force measurement frame, which measured the overall loads on the BargeRack.
The tests were performed in combined swell and sea waves from various directions with different wave periods, and significant wave heights up to 2.5m.
BargeRack concept
The concept may be compared to a forklift. The BargeRack lifts the feeder vessel completely out of the water and brings both the feeder barge and the BargeRack to a safe air gap above the waves. Accordingly, the installation of the components can be performed directly off the stationary barge, utilising industry standard static crane lifts. This results in much larger operational windows as compared to floating feeder solutions, which are weather dependent during the entire process, as described in a paper shared at the National Offshore Wind Research and Development Consortium 2022.
Risks due to vessel motions
“Typical feeder solutions are inherently risky due to vessel motions when equipment is being transferred. We’ve solved this problem by completely eliminating the feeder vessel motions, as well as reducing the cost by an order of magnitude compared to other feeder vessels,” explains Robert Clague, Vice President of Engineering at Friede & Goldman.
In order to further advance the technical readiness of the solution and confidence level for all stakeholders, concept verification model tests were performed in MARIN’s Shallow Water basin. The model tests focused on the lifting stage of the operation, when the feeder vessel is lifted out of the water. This is an unprecedented and the most challenging step in the BargeRack operation. The model tests provided verification of the concept and the operational limits of the system.
Friede & Goldman has developed its proprietary BargeRack system, which is a modular, safe, and cost-effective feeder solution for offshore wind installation, designed to comply with the US Jones Act. The BargeRack is a novel solution based on a lifting module concept attached to an (existing) Wind Turbine Installation Vessel (WTIV). The system can lift a feeder barge with wind turbine components out of the water, from which the components can be installed directly on the foundations from the fixed platform. The BargeRack solution avoids the hazards and risks that come with floating feeder solutions such as the frequent delays due to limited workability of floating lifts, dangerous offshore crew transfers and the double handling of components. Additionally, it doesn’t require customised, single purpose barges.
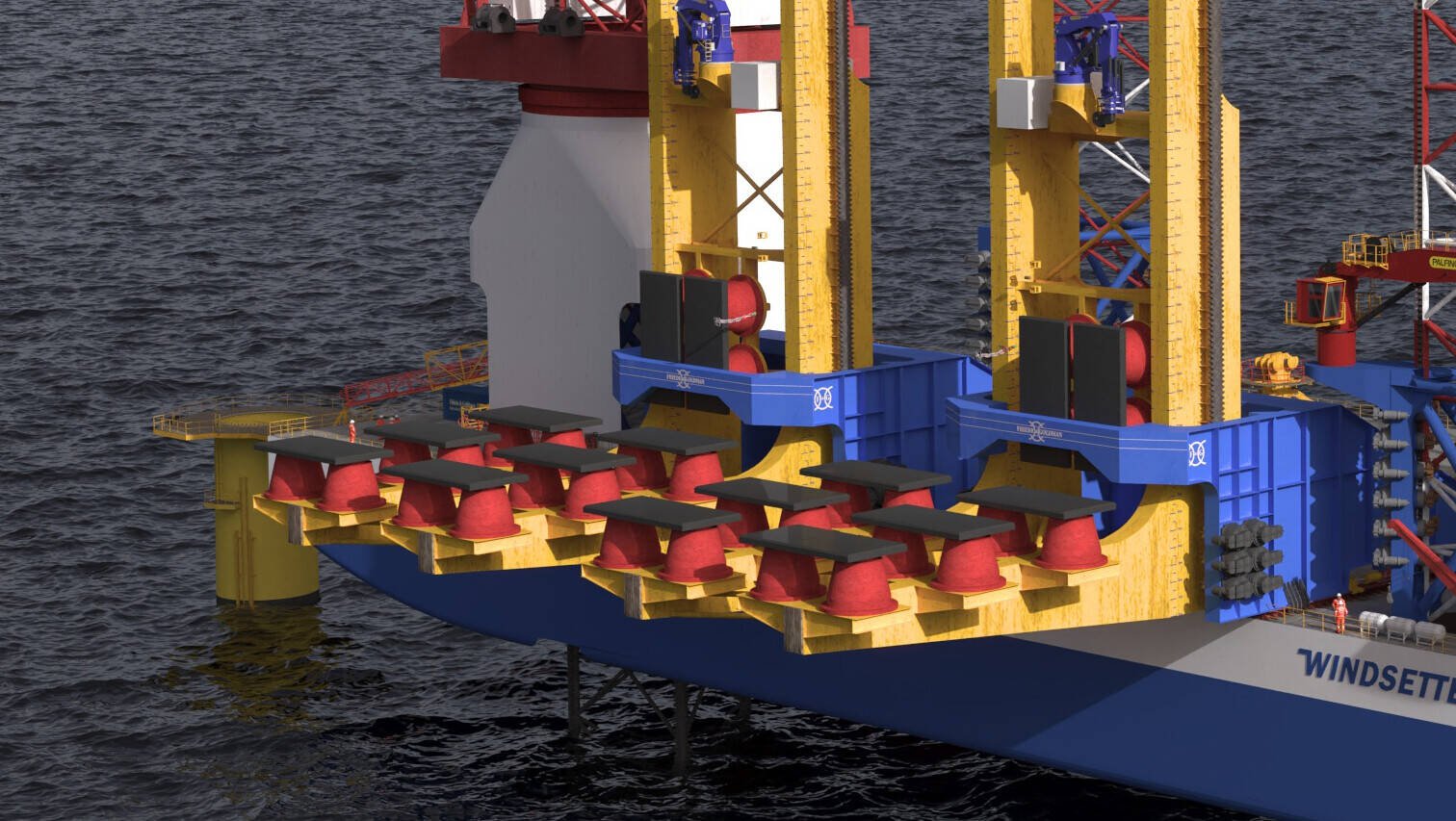
https://www.fng.com/bargerack/
More info
Figure 3: Barge and BargeRack models in the basin.
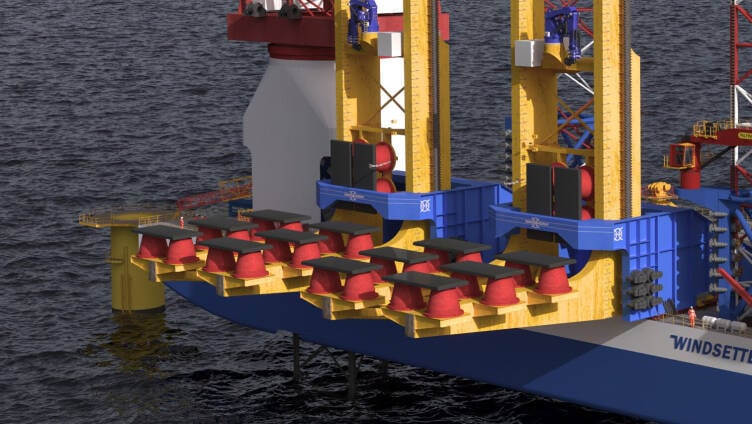
Figure 2: BargeRack model including vertical fenders (red) and horizontal fender system.
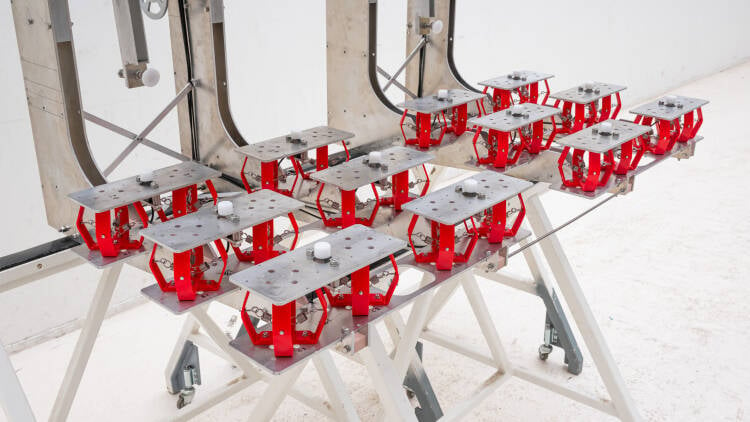
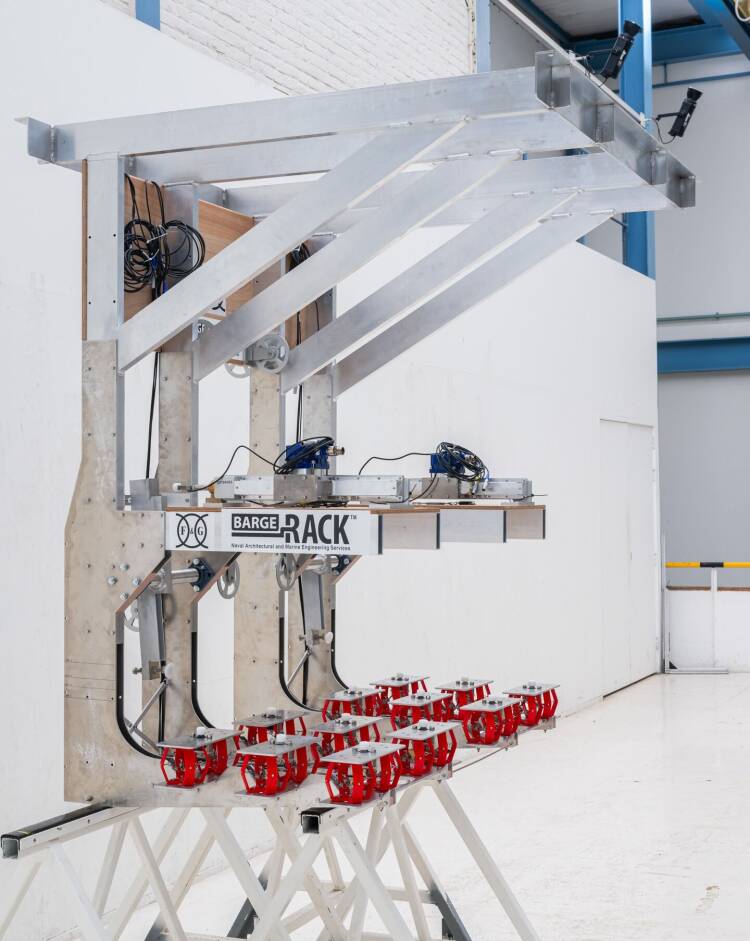
BargeRack concept
The concept may be compared to a forklift. The BargeRack lifts the feeder vessel completely out of the water and brings both the feeder barge and the BargeRack to a safe air gap above the waves. Accordingly, the installation of the components can be performed directly off the stationary barge, utilising industry standard static crane lifts. This results in much larger operational windows as compared to floating feeder solutions, which are weather dependent during the entire process, as described in a paper shared at the National Offshore Wind Research and Development Consortium 2022.
Risks due to vessel motions
“Typical feeder solutions are inherently risky due to vessel motions when equipment is being transferred. We’ve solved this problem by completely eliminating the feeder vessel motions, as well as reducing the cost by an order of magnitude compared to other feeder vessels,” explains Robert Clague, Vice President of Engineering at Friede & Goldman.
In order to further advance the technical readiness of the solution and confidence level for all stakeholders, concept verification model tests were performed in MARIN’s Shallow Water basin. The model tests focused on the lifting stage of the operation, when the feeder vessel is lifted out of the water. This is an unprecedented and the most challenging step in the BargeRack operation. The model tests provided verification of the concept and the operational limits of the system.
Figure 1: WTIV with the BargeRack Lifting Module.
Friede & Goldman has developed its proprietary BargeRack system, which is a modular, safe, and cost-effective feeder solution for offshore wind installation, designed to comply with the US Jones Act. The BargeRack is a novel solution based on a lifting module concept attached to an (existing) Wind Turbine Installation Vessel (WTIV). The system can lift a feeder barge with wind turbine components out of the water, from which the components can be installed directly on the foundations from the fixed platform. The BargeRack solution avoids the hazards and risks that come with floating feeder solutions such as the frequent delays due to limited workability of floating lifts, dangerous offshore crew transfers and the double handling of components. Additionally, it doesn’t require customised, single purpose barges.
December 2024, no. 142
Successful model testing
Impact loads measured during the model tests are in line with the results of the numerical simulations performed by Friede & Goldman. The concept verification model tests demonstrate the feasibility of the BargeRack solution and support Friede & Goldman in its development.
The successful completion of the model testing marks a major milestone for the BargeRack project. "We are excited to be one step closer to bringing this innovative solution to the market,” says Todd Allen, Director - Renewables at Friede & Goldman. “The success of the model testing reaffirms the significant benefit this technology can offer the offshore energy industry. The F&G team has worked closely with industry suppliers and fabricators to refine and ready the technology for deployment.”
Friede & Goldman have performed extensive hydrodynamic time domain simulations to determine the feeder vessel motions, dynamic impacts and the accelerations of the wind turbine components during the mating and lift. Structural simulations have been performed to guarantee the structural integrity of the BargeRack, feeder barge, and the WTIV. Earlier this year Approval in Principle (AiP) was received for the design.
More detailed insights in the BargeRack design and AiP assessment are given in Vidic-Perunovic et al. (2024).
Vertical and horizontal fenders
During the verification model tests the vertical and horizontal fender characteristics were represented in detail, as these are crucial for the motions of the feeder vessel and impact loads, while the DP system was not modelled and simplified by a string. The vertical fenders were 3D printed and represent the non-linear force-deflection characteristics of the full-scale fenders. The horizontal fenders characteristics were represented by active actuators.
The WTIV was not represented during the tests. Instead, the BargeRack was attached to the carriage by means of a force measurement frame, which measured the overall loads on the BargeRack.
The tests were performed in combined swell and sea waves from various directions with different wave periods, and significant wave heights up to 2.5m.
Interested? Contact us to discuss your options
The offshore wind industry is growing rapidly with an ever-increasing need for efficient, reliable, safe, and scalable installation solutions to help keep up with offshore wind developments. Compounded by port limitations, logistics bottlenecks, and cabotage laws there is more and more interest in wind turbine component feeder solutions to help meet this demand.
Concept verification model tests for Friede & Goldman’s BargeRack system
Create a MARIN account to stay updated
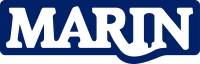
Report