June 2024, no. 140
The King experiences the unique opportunities of the Fast Small Ship Simulator.
www.marin.nl/fsss
www.marin.nl/sosc
More info
Interested? Contact us to discuss your options
FSSS / Fast Small Ship Simulator
Superyacht Times, How to build it
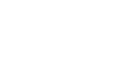

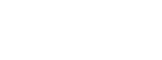
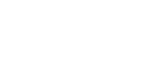

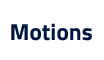

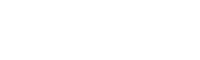
Create a MARIN account to stay updated
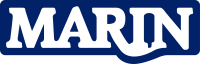
marin.nl/jips/toptier
Although rare, parametric roll has been identified as a key factor in container losses at sea. This phenomenon occurs when certain wave conditions align with a ship's natural rolling period, causing severe rolling within a short time frame. A recent study revealed that seafarers have a basic understanding of parametric roll, yet it appeared there is no consistency in prevention measures. Moreover, incidents confirm that parametric roll is a major contributor to maritime accidents and container losses.
Parametric roll is unpredictable and can quickly escalate to extreme angles. To address this, a research plan for a parametric roll experiment on the moving bridge simulator has been developed. By recreating realistic conditions, seafarers can experience and learn to recognise preconditions and prevent this phenomenon in a safe environment. In the summer a first study will be performed on the Large Motion Simulator as part of the Joint Industry Project TopTier to show how to effectively avoid extreme conditions like parametric roll. This study aims to improve understanding, decision-making, and response strategies for parametric roll incidents at sea.
Seafarers’ perspective on parametric roll:
a study on the Large Motion Simulator as part of the TopTier JIP
Report
Assess and feel the motions
Designing a ship or operation involves careful consideration of various factors. For a yacht the focus might be on ensuring comfort for passengers or crews, while for a containership the focus will be on the safe and efficient transport of goods.
Numerical analysis and physical model tests can provide valuable performance indicators for ship design. However, it is up to the crew to navigate the vessel safely in various conditions. With good seamanship, the operator will bring the ship, crew and cargo safely to its destination. But how can we better support the ship operators to navigate challenging conditions and enhance decision-making to optimise the effective use of the ship? And how can we utilise the experience and feedback of operators to improve the design of future ships? Especially when the motions influence the perception of the operator these are complex questions. This is where the motion-based simulators, the Fast Small Ship Simulator (FSSS) and the new Large Motion Simulator (LMS), offer unique opportunities.

Whereas traditional simulators are on a fixed platform, the motions of the vessel and their effect on the crew are now experienced on a moving base platform. These simulators provide a unique possibility to study the human factor in terms of comfort, sickness, workload and operating performance. Dedicated motion cueing algorithms translate the movement envelope of a real vessel into the less extended corresponding movement envelope of the simulators.
Ship handling in extreme motion conditions
Where mariners might have to wait a lifetime to experience certain extreme motions during the perfect storm at sea, it is possible to create specific very challenging conditions on demand in a simulator. This makes it possible to evaluate the effectivity of supporting measures, alternative procedures or training required. Additionally, simulators can play an important role in accident investigations.
The FSSS has already proven its added value in design decisions. For instance, by studying the influence on the behaviour of yachts with different stabiliser fins. In addition, the FSSS continues to provide a safe and accurate environment for training drivers and navigators of RHIBs.
With unique features for smaller/medium ships, the FSSS provides a 180° horizontal view, maximum roll angle of 27° and an acceleration of 1g (9.81m/s.). The new LMS is dedicated for medium to large ships. It provides a full 360° view, extended vertical view and motions up to 27° of heel. Additionally, all simulators can be coupled to the Multipurpose Simulators to allow for operations in which multiple operators are involved. With these new facilities MARIN’s capabilities regarding motions are extended significantly, contributing to our global mission of enhancing maritime safety.
Taking decisions in the selection of the most suitable stabilisation or steering systems, based only on numbers or suppliers’ information, is a recurring challenge for naval architects. They won’t be the one operating the vessel, but they are the one taking the decisions at an early stage.
Modifications or even substitutions of a stabilisation or steering system when the vessel is built can be a costly and detrimental operation. Involving the operators in the decision-making process is not only a way to share responsibilities, but also to take their valuable experience into the design itself when it is still possible.
The SOSc offers a range of simulators that enable this process of experience-based design decision-making long before the vessel is built. Real-time simulations to evaluate the most suitable steering systems to enter/exit a challenging port or perform an operation, is a largely underestimated activity that is now becoming accessible and part of the design workflow of high-end vessels.
Furthermore, experiencing the imposed motions on the Large Motion Simulator and Fast Small Ship Simulator obtained by computing or testing several stabilisation systems onboard, enable the stakeholders to take more informed decisions. When the roll reduction percentages are close to each other, is it really worth going for the more expensive, space and energy consuming system? Will you ever be able to feel the difference? To answer these questions comprehensively, jump aboard our motion simulators!
Incorporating operator experience in design decisions
Motion comfort as a design parameter
Motion comfort is very important for the performance of the crew. However, clear and unambiguous guidelines on what is actually considered comfortable movement behaviour are not available. By experiencing motions on a moving platform, it is possible to gain operator feedback in the early design stage. At MARIN we use advanced numerical models and the motion data from model tests to create the full experience.
Large Motion Simulator.
Large Motion Simulator.
Motion envelope.
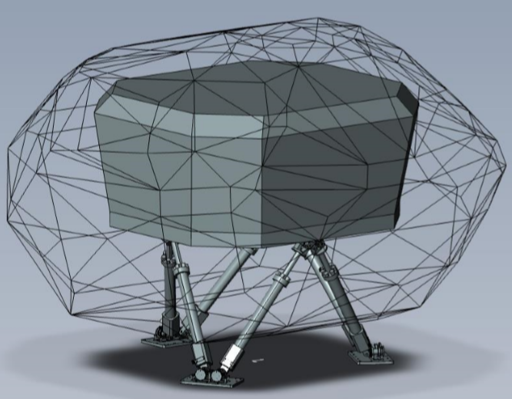
www.marin.nl/fsss
www.marin.nl/sosc
More info
FSSS / Fast Small Ship Simulator
The King experiences the unique opportunities of the Fast Small Ship Simulator.
Interested? Contact us to discuss your options
Superyacht Times, How to build it
marin.nl/jips/toptier
Although rare, parametric roll has been identified as a key factor in container losses at sea. This phenomenon occurs when certain wave conditions align with a ship's natural rolling period, causing severe rolling within a short time frame. A recent study revealed that seafarers have a basic understanding of parametric roll, yet it appeared there is no consistency in prevention measures. Moreover, incidents confirm that parametric roll is a major contributor to maritime accidents and container losses.
Parametric roll is unpredictable and can quickly escalate to extreme angles. To address this, a research plan for a parametric roll experiment on the moving bridge simulator has been developed. By recreating realistic conditions, seafarers can experience and learn to recognise preconditions and prevent this phenomenon in a safe environment. In the summer a first study will be performed on the Large Motion Simulator as part of the Joint Industry Project TopTier to show how to effectively avoid extreme conditions like parametric roll. This study aims to improve understanding, decision-making, and response strategies for parametric roll incidents at sea.
Seafarers’ perspective on parametric roll:
a study on the Large Motion Simulator as part of the TopTier JIP
Taking decisions in the selection of the most suitable stabilisation or steering systems, based only on numbers or suppliers’ information, is a recurring challenge for naval architects. They won’t be the one operating the vessel, but they are the one taking the decisions at an early stage.
Modifications or even substitutions of a stabilisation or steering system when the vessel is built can be a costly and detrimental operation. Involving the operators in the decision-making process is not only a way to share responsibilities, but also to take their valuable experience into the design itself when it is still possible.
The SOSc offers a range of simulators that enable this process of experience-based design decision-making long before the vessel is built. Real-time simulations to evaluate the most suitable steering systems to enter/exit a challenging port or perform an operation, is a largely underestimated activity that is now becoming accessible and part of the design workflow of high-end vessels.
Furthermore, experiencing the imposed motions on the Large Motion Simulator and Fast Small Ship Simulator obtained by computing or testing several stabilisation systems onboard, enable the stakeholders to take more informed decisions. When the roll reduction percentages are close to each other, is it really worth going for the more expensive, space and energy consuming system? Will you ever be able to feel the difference? To answer these questions comprehensively, jump aboard our motion simulators!
Incorporating operator experience in design decisions
Large Motion Simulator.
The FSSS has already proven its added value in design decisions. For instance, by studying the influence on the behaviour of yachts with different stabiliser fins. In addition, the FSSS continues to provide a safe and accurate environment for training drivers and navigators of RHIBs.
With unique features for smaller/medium ships, the FSSS provides a 180° horizontal view, maximum roll angle of 27° and an acceleration of 1g (9.81m/s.). The new LMS is dedicated for medium to large ships. It provides a full 360° view, extended vertical view and motions up to 27° of heel. Additionally, all simulators can be coupled to the Multipurpose Simulators to allow for operations in which multiple operators are involved. With these new facilities MARIN’s capabilities regarding motions are extended significantly, contributing to our global mission of enhancing maritime safety.
Large Motion Simulator.
Motion comfort as a design parameter
Motion comfort is very important for the performance of the crew. However, clear and unambiguous guidelines on what is actually considered comfortable movement behaviour are not available. By experiencing motions on a moving platform, it is possible to gain operator feedback in the early design stage. At MARIN we use advanced numerical models and the motion data from model tests to create the full experience.
Motion envelope.
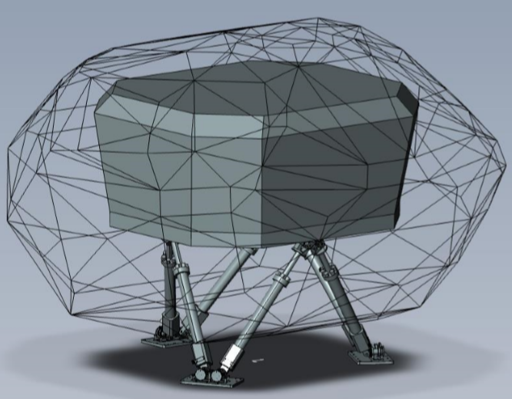
Whereas traditional simulators are on a fixed platform, the motions of the vessel and their effect on the crew are now experienced on a moving base platform. These simulators provide a unique possibility to study the human factor in terms of comfort, sickness, workload and operating performance. Dedicated motion cueing algorithms translate the movement envelope of a real vessel into the less extended corresponding movement envelope of the simulators.
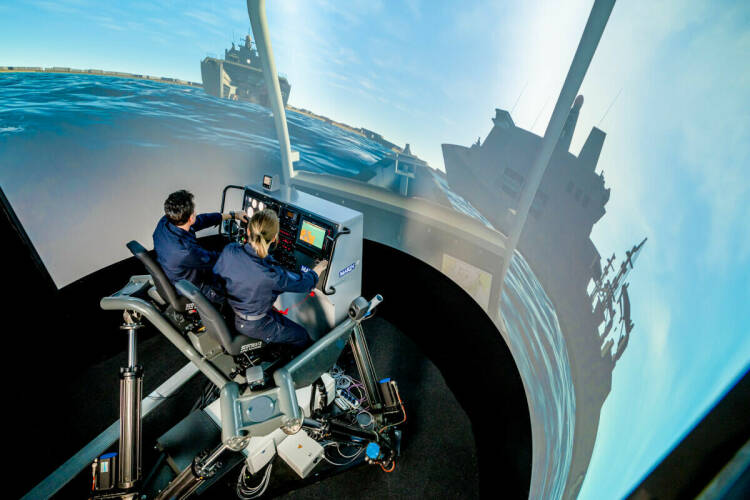
Ship handling in extreme motion conditions
Where mariners might have to wait a lifetime to experience certain extreme motions during the perfect storm at sea, it is possible to create specific very challenging conditions on demand in a simulator. This makes it possible to evaluate the effectivity of supporting measures, alternative procedures or training required. Additionally, simulators can play an important role in accident investigations.
June 2024, no. 140
Numerical analysis and physical model tests can provide valuable performance indicators for ship design. However, it is up to the crew to navigate the vessel safely in various conditions. With good seamanship, the operator will bring the ship, crew and cargo safely to its destination. But how can we better support the ship operators to navigate challenging conditions and enhance decision-making to optimise the effective use of the ship? And how can we utilise the experience and feedback of operators to improve the design of future ships? Especially when the motions influence the perception of the operator these are complex questions. This is where the motion-based simulators, the Fast Small Ship Simulator (FSSS) and the new Large Motion Simulator (LMS), offer unique opportunities.
Designing a ship or operation involves careful consideration of various factors. For a yacht the focus might be on ensuring comfort for passengers or crews, while for a containership the focus will be on the safe and efficient transport of goods.
Assess and feel the motions
Create a MARIN account to stay updated
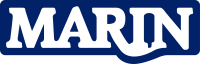
Report